A Tale of Two Quarries
Products
Following standard operating practices is easy to do, but when a quarry operation needs to improve plant performance, management must think outside the box, put aside misconceptions and consider the best technology to achieve its goals. For APAC Mid-South Inc., a leading supplier of aggregates, asphalt and construction services in the southeastern
United States, the switch to KPI-JCI Kodiak Plus® K300 Cone crushers proved profitable, with significant improvements in production, service and automation.
APAC Mid-South, an Oldcastle company with seven operating rock quarries and 26 asphalt plants in Alabama, southern Tennessee, Georgia and the Florida Panhandle, produces millions of tons of construction materials and paves many miles of highways every year.
The company was seeking to replace an old-style cone crusher and a horizontal shaft impact crusher in a limestone operation in Opelika, Ala. APAC knew it wanted to use the latest cone crusher technology which would improve plant performance, reduce fines production, reduce maintenance cost and provide automation control. At the same time, it was also looking for a new high-performance 8' x 20' triple-deck inclined screen with dual vibrators which would increase TPH and reduce operating costs.
According to Sam Reed, vice president of APAC Mid-South, he knew through his prior experiences with KPI-JCI and Astec Mobile Screens that the company offered quality equipment and service. While APAC Mid-South wanted to first compare all competing brands of cone crushers and vibrating screens, it ultimately purchased a Kodiak Plus® K300 Cone Crusher and KPI-JCI 8x20 triple-deck, dual-shaft inclined vibrating screen in 2010 for its limestone operation. "Unlike the old cone crusher, the Kodiak Plus® K300 Cone Crusher embodies the latest cone technology today," said Leon Luadzers, regional sales manager for Astec AggReCon South, a KPI-JCI and Astec Mobile Screens. "The Kodiak can be remotely adjusted and includes automatic tramp iron relief. The automation controls allow the operator to monitor the operation of the cone and to operate the cone at peak efficiency and capacity."
The Kodiak is the heaviest cone crusher on the market. Its balanced operating design allows it to work on old stationary structures and portable plants.
Part of the reason APAC Mid-South chose KPI-JCI as its supplier was because of the company's ability to provide a full range of aggregate processing equipment and offer a single source supply for its customers.
"We appreciated the fact that we could purchase both units from the same company," Reed said.
APAC Mid-South first replaced the old-style secondary cone crusher with the Kodiak Plus® K300, which improved plant production and uptime. Next, it replaced the tertiary impact crusher with a new Kodiak Plus® K300 Cone Crusher and found it was making 50 percent more 1/2" and 3/8" rock than before. This was one of the major goals and it exceeded the company's expectations. The two Kodiak Plus® K300 cone crushers are actually identical units except for liner configurations. The Kodiak cones are available with a wide range of liner choices, which make them versatile and allow them to be utilized in primary, secondary and tertiary applications.
The new KPI-JCI 8' x 20' triple-deck dry screen was installed and it improved screening performance and it handled the increased tonnage. A new KPI-JCI 8' x 20' triple-deck wash screen was later installed and it improved production of washed rock products.
In another quarry 50 miles away in Alex City, APAC Mid-South was determining which manufacturer to use to replace an old cone crusher. But instead of limestone, the company was crushing granite – and it wasn't sure if a roller-bearing cone crusher could perform well in a granite quarry.
"It takes a really good crusher to crush granite," Reed said. "To be honest, roller-bearing cones just don't enjoy the same perception as brass (bronze bushings) in the South, so we were hesitant to try it in a different application. But it was a great guarantee- we knew if it didn't work out, KPI-JCI was going to take care of it."
OVERCOMING MISPERCEPTIONS
The misperception that roller bearing technology is inferior to bushing designs is one that is often purported by other manufacturers. But there are significant advantages of how a roller bearing absorbs crushing loads versus sleeve bushings, including:
- A 360-degree loading situation with millions of
points of contacts that are constantly changing - Higher productivity with a lower cost of ownership
- More saleable net product and more efficient
power consumption - The ability to run at higher operating temperatures,
thus requiring less oil conditioning - Longer life of wear parts, which ultimately reduces
the cost in replacement parts
"We have put our roller bearing cone crushers in a variety of hard rock applications and they have excelled in each one," Luadzers said. "The reality is that the Kodiak is well-suited for the Southeast and elsewhere, as it is the heaviest built cone crusher, has the widest temperature operating range, the most productive and balanced design, automation controls and standard anti-spin design."
For a complete technical overview on the differences between roller bearing technology and bushing designs, see sidebar story.
EXCEEDING EXPECTATIONS
APAC Mid-South asked if it could visit a granite quarry using the Kodiak cone crusher and a visit was arranged with a granite stone producer in North Carolina who had been using Kodiak® crushers for 10 years. Reed was convinced that the company should try the Kodiak Plus® in its granite application and he believed it could achieve equal, if not better, results. The company wasn't disappointed. Steve Horne, senior production manager at APAC Mid-South, said the crushers have proved to be high-performing machines in both applications.
"We had two different sites with two different requirements, and all three crushers have done what they're supposed to, Horne said. "We wanted a machine built of heavy-duty steel that could withstand the rigors of our industry, and that's what we've got. The new crushers have helped us increase our production and uptime, while decreasing the amount of fines produced."
In addition to the improved production, Horne said APAC Mid-South has found that the Kodiak Plus® K300+ Cone Crusher has been a less expensive machine to operate. By properly maintaining the equipment and regularly examining the inside of the crusher, the company has reduced the amount of replacement parts needed and lowered maintenance costs.
"We're making sure that our maintenance practices are conducted according to the kind of rock that is being crushed," he said. "You can't expect a crusher to hold up when you don't practice proper maintenance. If your people don't look after your equipment, things are going to go wrong."
The company hopes to continue to standardize equipment across sites, which will lead to improved efficiency and employee training.
"We want consistent products," Horne said. "We also want to have common products to make stocking inventory and training for employees easier. Our goal is always to streamline our operation and maximize our production, and I think we're accomplishing that."
Find Astec product availability nearby
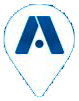