Assembly Yard
Products
The first time Tony Bradley, Crushing Superintendent for Brent Scarborough & Company, set foot on this job site was actually decades before the project started. During a high school field trip, he visited the General Motors assembly plant that formerly occupied the 125-acre (0.5 km2) campus. Today, he is helping transform the remnants of that manufacturing hub into something entirely different. A new industry is taking root - the film industry.
When Bradley first heard about the ambitious redevelopment project in Doraville, just north of Atlanta, Georgia, USA, he was impressed with the size and scope of the job. A parcel that formerly housed the automobile assembly plant would be transformed into a mixed-use site that would include film studios, commercial real estate and park space connected to nearby neighborhoods. It called for recycling a large majority of the existing on-site material.
By recycling materials already on hand, Brent Scarborough & Co. was able to keep material out of landfills, avoid the costs and emissions of transporting new materials to the site and preserve natural resources.
In a nod to the site’s history, where cars once rolled off the assembly line, the new campus will be known as ‘Assembly Yard’. Except now, it will be a place for community connection and art creation.
The Company
Brent Scarborough & Company is one of the largest heavy civil site contractors in Georgia. Started in 1985 as an erosion control company, their work has expanded to specialize in clearing, grubbing, grading, boring and underground utilities. The company, which is 100% employee-owned, executes projects throughout the Southeast United States.
Equipment
Breaking down nearly 225,000 yards of concrete and rock while staying on schedule requires heavy-duty power and durability. Bradley looked to Zack Gradwell, Vice President, Environmental Solutions Group at Stone Equipment Co., to supply the right equipment for the job. In this case, a closed-circuit FT4250CC mobile HSI plant and FT2650 mobile jaw plant.
“The 4250 is a brute of a machine,” says Gradwell. “This job site contains some gnarly material; a lot of dowel rods and chunk metal. The solid steel rotor on the 4250 is able to keep up with that and combat it with minimal damage, if any.” Gradwell goes on to compare Scarborough’s previous equipment selections, “They had a competitive machine out there that just fell apart every week or so while they were waiting for the Astec machine. It definitely combats the metal, the recycled material and is also good on fuel. They see pretty good fuel [consumption] for the tonnage that they’re running, so it’s been a good all-around machine for them and this application.”
“We bought the FT2650 jaw about four years ago. That was the first one we purchased. Since then, we have purchased two GT125 jaws, two GT165 scalping screens and then we bought the FT4250 impactor plant,” says Bradley.
The crushing power of Astec equipment has kept the multi-year project on track. “The FT4250 usually runs at around 250-260 tons per hour. The FT2650 will produce about 225 tons per hour. That’s in a six-inch-minus rock. This makes an inch and a half minus rock. The four-inch-minus material usually runs about 225 tons per hour as well,” according to Bradley.
As for his favorite features, Bradley says, “I’m partial to the solid steel rotor on the mobile HSI plant. It’s been heavy-duty and durable for us. We also love the screen box on it, specifically the distance between the screen box and the under-crusher belt. We just like the machine overall. Astec is just where we want to be. It’s been the machine for us,” says Bradley.
Power and ruggedness aren’t the only reasons Scarborough continues to rely on Astec machines. On a jobsite where multiple operators need to be able to work with different types of equipment at any given time, it is a huge time-saver to have user-friendly equipment.
“They have different operators operating 2650 jaws, 125 jaws and 165 screens,” says Gradwell, “They can all jump from one machine to the other without any problems or hiccups. And if there is something they don't know, they can call either myself or a product support rep at Stone Equipment Co. and we can get them going right over the phone. It’s just that simple.”
This same customer-centric support from Stone Equipment extends past just parts and service. They also encourage onsite and online training opportunities. “We put the operators through training on site,” says Gradwell. “We encourage them to go online and do the Astec training to better familiarize themselves. We also work with their mechanics because that’s where you need the support for these machines. They need be able to fix it themselves.”
“The support from Stone Equipment has been great,” says Bradley. “We couldn’t ask for better service from them. They have quick turn-around times on parts and do their best to keep everything we need in stock locally. “
Challenges
You never know what to expect with a demolition job. Depending on the site, workers can encounter all kinds of challenges from unexpected materials to unsafe conditions.
“The strangest thing I ever found on a jobsite was a cement truck buried 12 feet in the ground. To this day, that was the most challenging item I’ve encountered on a demolition job. Fortunately, we haven’t come across anything so unexpected on this site. We have encountered a large mix of materials while demoing the former car factory. We’ve been demoing the flat work that we can see, we’ll hit a wall and dig down, then maybe 8-12 feet later we find another slab and the walls of a previous building. We process it down and try to get all the rebar out first. Getting it out of the ground and getting it to the crusher has been more of a challenge than crushing it,” explains Bradley.
The process is rigorous, but throughout the job, the Astec crushers have effortlessly pivoted between various materials.
“Here, we have everything from lime rock, limestone, to granite, and you'll hit different kinds of concrete made out of these materials,” says Gradwell. “It's different materials in the field and these machines are able to jump from one to the next. We’re able to set them up from doing asphalt to concrete, from hard rock to soft rock. Astec crushers can tackle a number of different materials with ease.”
Astec Relationship
The company focus on quality Rock to Road® solutions extends beyond the equipment. When Gradwell thinks of Astec, he thinks reliable. “You call them and get what you need. You talk to somebody that you can build a relationship with. I’ve made friends with pretty much everybody in the service department because we called them a lot in the early stages of our business. Those guys really helped us; we know the parts department like family. And then our customers join the training at the factories, so it’s all been a lot of help. It’s been a great relationship with Astec.”
While the project will extend into 2024, studio production on site began in the third quarter of 2023. Astec machines will still be on hand, doing their part to bring the historic materials of the past into the future.
Find Astec product availability nearby
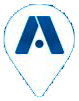