Astec Burner Options for Retrofit Applications
There are many factors to consider when choosing a retrofit option and the team at Astec can help
Asphalt plant owners are always looking for ways to improve plant performance. As tried and true plant components start to wear out or become obsolete, plant owners need to consider retrofit installs. One the most critical components to consider for upgrade is the aggregate drying burner. Reliable burner performance is at the heart of a successful asphaltic concrete production facility.
Selecting a new burner for your plant comes with several considerations before the replacement can be made. For example, you need to consider spacing issues, changing emissions requirements, permitting and much more before an install can take place.
Having the right partner who can help you through this process from start to finish will help ensure your operation will be back up and running in no time.
The Right Fit
Since your burner will last you a long time, you want to make sure you’re choosing the right one. First, one must consider the burner’s compatibility with existing equipment. The burner engineers at Astec are available to help. A thorough evaluation of plant operations is key. Heat and airflow requirements for production must be calculated. The team at Astec can provide detailed heat and mass analysis on plant operations to ensure you make an informed decision. Through this analysis Astec engineers will evaluate the existing exhaust system capacity relative to the new burner’s requirements.
Astec engineers will always recommend an appropriately sized burner for your plant based on your drum and baghouse size so that plant output is always optimized. As part of this process, engineers will try to be forward thinking for plant owners, making sure they do not have plans to change the size of either of these components in the near future so that the burner will still be the right fit.
Once that’s determined, the engineers will ask more questions about your plant to make sure there is enough space for your new burner in the existing location. For instance, if you have a very short platform on your drum, there may be a space issue that you're going to need to address. It could be that you need to extend the drum frame to overcome installation obstacles or find another way to get that burner to fit.
Engineers at Astec may conduct a site visit to the plant to help establish the exact needs of the plant and burner location. This is especially true if an Astec burner is being installed on a different brand of asphalt plant.
A site visit will also allow engineers to take photos and dimensions of the burner platform to make sure it will accommodate the new burner or if modifications need to be made. Doing so will identify potential obstacles with installation ahead of time which helps ensure everything with the new install will go smoothly and fit correctly once the time comes, eliminating the chance of excessive downtime.
Burner Design Matters
All Astec burners offer the latest in reliable burner technology combined with complete one-source responsibility. With retrofit capabilities, Astec is able to offer everything from a simple burner replacement to a complete installed system. While any burner can be utilized in retrofit applications, Astec saw an opportunity to create a burner that was specifically designed for retrofits.
When creating the new Astec Versa Jet™ burner, Astec engineers reimagined the asphalt plant burner to create a new system that takes an evolutionary leap forward. The Versa Jet burner is different from current burners that Astec offers. The Versa Jet is a total air burner, but it also has very low differential pressure across it. This means the burner is able to provide a higher heat output with lower horsepower.
The Versa Jet burner features a straight cylinder design which gives the burner the ability to be used on very low platforms. Unlike a burner that points up or down, this configuration also allows the unit to be set up more quickly at the plant.
Fuel trains also matter in retrofit applications as most burners come packaged with the fuels trains already assembled, mounted and wired together. In a retrofit situation however, many plants may already have functional fuel trains that don’t need to be replaced. The Versa Jet burner was designed with this in mind, without the fuel train automatically attached. This configuration gives plant owners flexibility and versatility they may not have when using other comparable burners in retrofit applications. They can purchase a fuel train from Astec either assembled with the burner or as a separate kit. The plant owner can also choose to or use their existing, functional fuel train system.
The Versa Jet is compatible with virtually all drum designs without complicated drum modifications and has the ability to work with existing controls. It can also be easily relocated to a different plant and its maximum output changed if the need arises.
Don’t Forget About Emissions
When installing a new burner, your company will need to make sure it will pass all emission requirements.
Upgrading the burner often requires a permit modification which may trigger additional restrictions. State and local governments dictate the plant’s emissions requirements and not all burners will meet all the requirements. Astec has an experienced permitting consultant who is available to help you evaluate current regulations before making any decisions about a burner upgrade to ward off far-reaching and unintended consequences. A good permitting consultant and qualified plant equipment manufacturer, working together, can make the otherwise daunting task of upgrading an existing system with a new burner much easier. The decision to upgrade the burner often brings about permitting requirements that may be costly. When emission standards dictate the need for a burner upgrade, evaluating the entire facility, particularly the heat and airflow requirements, is vital to making the best choice.
Parts & People Matter
At Astec, our customer’s needs always come first. Our staff is on hand to assist plant owners and operators from the beginning of a purchase to the end, and beyond. We will make sure you choose the right product for your application, build the product in our state-of-the-art facility to your specification, help get it to you as quickly as possible and ensure we have service personnel available to help you get the burner installed and get you up and running.
We know plant owners have a choice in their purchase, but at the end of the day, you’re not just getting an Astec product, you’re also getting our expertise. We have cultivated 49 years of expertise in the asphalt plant industry and with that, over 20 years of knowledge building burners.
Find Astec product availability nearby
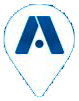