Beyond Your Average Monitoring Tool
Highlights
The Astec IntelliPac Moisture system is equipped with advanced features that empower operators with real-time data and enhanced visibility into virgin aggregate moisture levels to allow for a more precise addition of liquid asphalt cement, ensuring optimal asphalt mix consistency.
Products
Picture it: It’s a typical day, the plant is shut down, everyone’s left for the night and you’re feeling good.
Then it starts to downpour.
The next day, the plant is up and running before anyone can measure moisture levels resulting in more liquid asphalt being used than necessary. By the time the crew can recalibrate, the losses are already tallied.
That’s just one example. Situations where plants are not operating with the most up-to-date data happen all the time and unfortunately, those miscalculations can really start to add up and take away from your bottom line.
Seeing the need for reliable, real-time data, Astec developed its IntelliPac™ Moisture System, empowering operators to make on-the-fly adjustments, creating a dynamic and responsive asphalt production environment.
Behind the development Astec IntelliPac Moisture System
The Astec IntelliPac Moisture system is equipped with advanced features that empower operators with real-time data and enhanced visibility into virgin aggregate moisture levels to allow for a more precise addition of liquid asphalt cement, ensuring optimal asphalt mix consistency.
“When we provide a moisture sensing solution, it truly is a solution not just a standalone sensor,” says Trevor Wagoner, Astec’s director of sustainability. “It’s integrated into our control system. You're not relying on an operator to look at a moisture value up on a screen and then decide to make changes at a plant, we're automatically making those changes.”
This integrated approach takes the guesswork out of the process, ensuring that the best possible outcome is achieved every time.
To make this possible, there are two key aspects of the system.
The sensors
Conscious of the needs of the industry, the Astec team took on the task of evaluating several types of sensors to determine each’s effectiveness when faced with the heavy-duty wear process of an asphalt plant environment. After two years of rigorous testing for accuracy, calibration and durability, the team felt confident that two sensors were up to the task.
“It’s a very abusive, challenging environment for any sort of technology to live so we wanted to make sure that the sensors that we were testing were not just going to measure moisture, but that they were going to be able to do so reliably and accurately over a long period of time,” says Wagoner.
In the course of its extensive evaluation of different sensors the Astec team identified two that rose above the rest, a noncontact sensor and a contact sensor.
The Astec team felt confident in selecting a noncontact sensor as the preferred sensor to support the IntelliPac system. Compared to many of the moisture sensors on the market today, there’s an inherent advantage here as it’s never touching the material and not wearing down at an accelerated rate.
“The biggest differentiator is that we are an OEM that's supporting this, so you get all of the benefits that come with it being fully developed into the rest of our platforms,” adds Wagoner.
An additional perk – routine maintenance is simple. The biggest maintenance requirements are wiping the lens on a routine basis to make sure the sensor is clear and changing out the lamp bulb that emits the light to measure the moisture off the material.
The Astec team is confident in the durability and the accuracy of the sensor readings, however, as a noncontact sensor, there is still some risk and additional maintenance may be necessary.
The Astec team also has a high level of confidence in the readings provided by the contact sensor it offers as an alternative to the non-contact sensor.
Data logging
One of the other key features of the system is its comprehensive data logging functionality. The system records virgin aggregate composite moisture levels, enabling operators to track and analyze historical trends to make smarter decisions.
Accurate moisture content in the materials that are coming into the plant is critical to the plant's ability to dose liquid asphalt into the mix. If your moisture is high or low, you're going to under or overdose liquid asphalt into your mix, which can have negative impacts on your business. If you're overdosing, you're wasting liquid asphalt, the most expensive ingredients in an asphalt mix. However, if you underdose, producers can get severely penalized for not putting enough binder into their mix.
“Most producers will err on the side of overdosing their liquid asphalt which presents an opportunity for a real-time system like this to give that operator the tools that they need to actually run more accurately,” Wagoner continues. “Having that data and having access to it in real-time, not just whenever the lab guy has time to go measure the moistures in the stockpiles, lets the plant keep up with natural fluctuations in moisture in their materials or correct the action of the loader operator.”
Correcting big day-to-day swings is only part of the story. This data allows operators to have more consistent and uniform production throughout the entire day.
Overcoming labor shortages
Manufacturers tend to recommend that lab personnel take moisture measurements at least once per day, if not more. Though realistically, that’s a rare occurrence.
The Astec team designed this system in a way that is easily used by individuals with differing experience levels.
“The most successful products are the ones that are the most intuitive and easy for the end user to navigate,” says Wagoner. “We don't want people to have to flip through a textbook every time they want to calibrate the system or figure out what they're supposed to do with this weird number that's showing up on their screen, we want it to be very intuitive and easy to use.”
With labor shortages throughout the industry, it’s essential that we find a way to bring in the next generation. Combine that with the fact that there’s a shrinking supply of experienced operators in the field - the individuals who developed a gut feeling for determining things like moisture levels – things need to change.
Many plants are welcoming fresh faces on site, even recruiting from outside the industry. Which is a great step, however getting new crew members up to speed takes time, and in some cases, money.
“The problem is that playing it safe is really expensive because playing it safe typically means they're putting too much liquid into the mix,” adds Wagoner. “We're not just saying ‘use the system, reduce your liquid asphalt,’ we're saying, ‘use the system, run your plant more accurately, produce a higher quality mix, don't waste material, take advantage of the operators that you have and don't burden them with having to go through this incredibly time-consuming process of measuring stockpile moisture.’”
Introduced at World of Asphalt 2024, the IntelliPac Moisture System sensors can be tailored to meet the specific needs of your plant.
![]() |
IntelliPac™ Installation The system is installed on the cold feed bins. Producers then only need to calibrate the sensor for the material that’s in the bin. If you change the material that's in the bin, you can change the calibration, each sensor can save a whole host of calibrations. PRO TIP: make sure that you've got a moisture sensor on the fine material. That's where most of the variability is going to be.
|
Find Astec product availability nearby
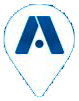