Building Complete Trust in Asphalt Production
Highlights
Country / Region | USA |
---|---|
Installation Site | Noblesville |
End User | E&B Paving |
PLANT STYLE | Relocatable |
Application | Asphalt Mixing |
DRUM STYLE | UniDrum |
Tonnage | 500tph |
Since 1967, E&B Paving has been serving the Northeast Indiana asphalt market with a broad range of road construction services. Like many companies, founders Jack Euratte and Richard Bedwell started small with one asphalt plant located in Muncie, IN, but that quickly changed.
By 1986, E&B Paving owned ten asphalt plants which included their first portable plant which they purchased for an $8.4 million resurfacing project on U.S. 30 in Whitley County, IN. – the single largest contract in the company’s history to that point. They also acquired Acme Paving Co. and its five asphalt plants that year.
Growth like this doesn’t just happen by accident. It comes from hard work, dedication and partnering with the right companies who are also dedicated to your success. This is why E&B Paving has relied on Astec, Inc. asphalt plants since the very beginning.
“We have a very long history with Astec and have basically grown up with their company,” Brian Crume, asphalt production manager at E&B Paving says. “We started in 1967 and they started in the early 70’s so we’ve had a long partnership with the company. Their products are very high-quality and they always stand behind their service. They’ve always been really good at helping us out and we’re very comfortable that they can meet our needs.”
New Location, Another New Astec
So when E&B Paving was looking to replace a plant that was nearly 50 years old for their Noblesville location, it was no surprise that they turned to Astec, Inc.
“Our Noblesville plant was one of our oldest in the company and it had a pretty small footprint,” Crume said. “We were sharing property with a stone quarry so when we wanted to upgrade it, we knew we needed more space.”
The company chose a new location just 3500-ft. away from the old plant to install a much larger production facility that would meet their growing needs.
“The old plant was a late 1970’s vintage Astec wet-wash that could only produce around 200-220 tons per hour,” Crume said. “The market in this area has grown considerably since then and the surrounding area is growing out towards us as well. In order to take care of additional business opportunities, we needed a larger plant.”
In fall of 2018, E&B chose to install a new Astec, Inc. plant featuring a UniDrum counterflow mixer rated at 500-tph.
“We like the simplicity of the counterflow drum,” Crume says. “We have some parallel flows and we have several Double Barrel plants and we also have a couple of older counterflows and we really like the simplicity and efficiency a counterflow offers and decided to go that direction.”
At this location, E&B produces mix for the Indiana Department of Transportation as well as Federal Highway work. Crume says they also make mix for commercial and private work and sell a fair amount of pickup to lay down customers. With the new install, Crume says they are much better equipped to meet the needs of the customers in that area.
“We have more aggregate bins and more recycle bins now so we have the ability to have more products on hand ready to put into the mix without cleaning out bins and taking time doing that,” he says. “We also have more storage capacity with our four 300-ton silos now and a dual scale instead of a single scale. This allows us to make a larger number of mixes, a larger quantity of those mixes and we can get people through the scales more efficiently than we could before.”
Partnering for Success
When completing a massive new plant installation, having the right partner can make all the difference, especially when working to overcome challenges together.
E&B had been struggling with a means to efficiently heat their emulsion and turned to Astec and Heatec for help with a solution.
“Normally you're just using the same oil that you heat the plant and your liquid asphalt tanks with and that oil really is a little too warm to heat emulsion or tackcoat,” Crume says. “We expressed our concerns with that and Heatec was able to provide a means to heat our emulsion with a much lower temperature oil than we traditionally had."
Heatec installed a system that allows the new location to use the return oil to heat the emulsion. The system is on its own thermostat so it's metered and adjusted which keep the heat in the emulsion tank tailored to the right temperature.
While Crume says that was one bonus of the new location, another was a shorter install time. The new plant has now been up and running since April of 2019, but that could have been delayed much longer without the help of the Astec team.
“This was the first time we relied on outside help to install one of our plants,” Crume said. “We had Astec come and complete the install for us because we didn’t have the resources and manpower at the end of 2018 to get it done.”
The Astec team was able to start the installation process in October of 2018 where the E&B team would have had to wait to start installation until their work was done in December.
“We were we were extremely happy with the quality of their work and the timeliness of the install,” Crume says. “If we found something that we needed them to address, they took care of it right away. We just had a had a really good experience with having them install the plant.”
Find Astec product availability nearby
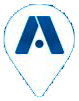