Changing the Game
Products
Couch Aggregates Doubles Down on GT205 Multi-Frequency Screen.
Todd Barnes has two rules for his wash plant at Couch Aggregates’ sand and gravel operation: More pay product, less fine sand waste.
Barnes, who is plant manager for the dry mine facility in Jackson, Alabama, fights a daily battle against the mine’s high-moisture, clay-rich aggregate and organic material. The unwanted sand and woody waste are costly barriers to maximum productivity, adding unnecessary expense from wear, fuel and handling of material.
In early 2017, Couch Aggregates conducted side-by-side testing of two industry-leading mobile screening plants. The company ultimately chose to buy two GT205 Multi-Frequency Screening Plants from Astec Mobile Screens, which gave it the ability to scalp off the oversize rocks and organic material, remove the unwanted fine material and capture an intermediate product of ¼” by 2” rock.
The GT205 Multi-Frequency Screen is a 5’ x 20’, track-mounted plant featuring a conventional screen on the top deck and high-frequency screen on the bottom deck. The unique combination of high frequency and conventional screens in one self-contained unit puts more energy into the screening process, creating a powerful machine capable of increasing capacity by up to 50 percent on the bottom deck.
“It’s a game changer in the sand and gravel market,” said Zack Gradwell, Georgia sales manager for Stone Equipment Company, who worked with Couch Aggregates to help the company find the perfect screening tool for its operation. “The GT205 Multi-Frequency Screen handles nasty material better than any screen I’ve seen. We’ve had competitive units out here and none of them were able to put out the production we’ve been able to put out in this sandy, wet, clay-rich material.”
Couch Aggregates is a leading producer of fine and coarse aggregates in Alabama and northwest Florida. The company has operations in Jackson, Tuscaloosa, Montgomery and Dothan, Alabama, as well as operations in Panama City and Walton County, Florida. It supplies materials for a wide variety of markets, including ready-mix and asphalt producers, general contractors, landscapers, masons, golf courses and grading contractors.
When the company began looking at equipment that could relieve the burden on its main wash plant, it chose Astec because one of the company’s partners had experience with Astec Industries equipment and Stone Equipment Company.
“We already had a pre-screener on site, and so we had it go head-to-head with the GT205 Multi-Frequency Screening Plant to test its abilities,” Barnes said. “The multi-frequency screening plant outperformed our existing plant, allowing us to get more of a usable product to our washing area and leave a lot of the material that we don’t sell.”
Gradwell said the previous screening unit Couch Aggregates was using – a comparable 5’ x 20’ mobile screening plant from an industry-leading manufacturer – was producing 80-90 TPH, whereas the GT250 Multi-Frequency Screen produced 135-140 TPH in the same conditions. But the real difference lay in the cleanliness of the product.
“The GT205 not only produced 60 percent more product, but the material was also so much cleaner,” he said. “The competitive unit was able to get up to almost 100 TPH, but it just became real dirty with a lot of blinding and runover – basically just a lot of unwanted sand, which is not what they were looking to achieve.”
By using the GT205 Multi-Frequency Screen, Couch Aggregates increased production by 20 percent and reduced unwanted fine material going to the settling ponds by 10-15 percent, in addition to cutting down on fuel costs and increasing handling efficiency by up to 300 percent, Barnes said.
“The screen on the GT205 plant has outperformed the other ones we’ve tried,” Barnes said. “It’s a fairly simple design, which makes it operator friendly. They’re dependable machines that give you very little trouble. You come in the morning, check everything out on them, make sure everything is topped off and tightened down, and you go to work with them and they work all day.”
Couch Aggregates’ Jackson operation runs year-round with a team of 26-32 people and produces about 700,000 tons per year, Barnes said. Out of that material, 60 percent is a #67 aggregate, 20 percent is a pea gravel and 20 percent is oversize aggregate that is sold as a metallurgical rock.
The material is mostly composed of a heavy iron stone, or sandstone. The material starts as a 60/40 sand-and-gravel mix, and Barnes seeks to achieve a 40/60 sand-to-gravel mix before the material is run through the wash plant. The larger material is scalped off to prevent damage to the wash plant. Some of the material has a heavy clay base, which tends to stick together, so Barnes and his team work to screen out the larger clumps of clay to just get the usable material they need for the wash plant.
“We deal with a couple of different clay bases in various spots at the mine,” Barnes said. “Some of it is a blue-gray, thick, gummy clay. Some of it is a chalky clay, and that’s scattered throughout the whole job site. It changes about every 100 feet, so you’ll never dig in the same substance twice. These are just obstacles we have to learn to overcome.”
Barnes also combats unfavorable Alabama weather – long, hot summers, cold, short winters and an abundance of rain year-round.
“It rains a lot here, and whenever the material gets wet, it’s harder for us to do some of the dry screening,” Barnes said. “We try to keep a good pile of material on higher ground so that whenever it does rain, it has a way of draining out so that we can keep the dry material going through the screens. But the wet material actually does really well with the GT205”
The operation’s production begins by clearing the land, then bringing in the screening plants and placing them as close as possible to the mining operation. Since the GT205 Multi-Frequency Screen is portable and self-contained, it’s easy for Barnes to move around in the pit, going from one side of the quarry to the next in a matter of minutes, he said.
After mining the rock, the material is pre-screened to remove as much sand as possible from the product, which is then run through the wash plant. The product is separated into four categories: sand, pea gravel, #67 and #57. From there, the sized material is hauled to a site on the river and conveyed onto a barge, where it is delivered all along the East Coast and down into the Florida Panhandle.
The GT205 is the first multi-frequency screen to hit the market, and was launched in 2015 by Astec. Multi-frequency screens blend the technology of conventional incline and high frequency screens to create a screening tool that increases fines separation, according to Stephen Whyte, Fast Trax and Global Track product manager for Astec.
Conventional incline screens function by applying a lower speed (900-950 RPM) and increased stroke (1/4”-3/8”) to the entire screen box to convey the material down the screen and maintain consistent bed depth. This applies up to five g’s of energy into the material. High frequency screens apply high speed vibration (3,600-4,200 RPM) directly to the screen media to allow for increased stratification and separation of material.
The GT205 Multi-Frequency Screen combines the two screening theories to produce a one-of-a-kind vibration that applies 15 g’s of energy to the bottom screen deck and creates a versatile screen prepared to tackle any application.
“The GT205 Multi-Frequency Screen allows producers to process finer materials with higher moisture content that no conventional screen could process, all while being operated at a lower angle than a high frequency screen,” Whyte said.
Barnes said his team typically pushes at least 1,500 tons per day through the screening plants, which allows them to get between 800-1,000 tons of usable material to take to the wash plant. They keep the remaining 500-700 tons of unusable material in the mining area to use for reclamation instead of hauling it to the wash plant and straight back again.
“These guys push the machines really hard,” Gradwell said. “This is a tough, robust machine. These plants run sometimes 24 hours a day, seven days a week. This machine stands up to some really, really high temperatures, some really high-productive scenarios and situations, and it just keeps producing.”
In addition to the increased productivity and cleanliness of the material, Barnes said he appreciates the simplified design and ease of maintenance, as well as the assurance of having parts and service readily available.
“Changing the screens out is really easy. I can usually take a greenhorn and put him with a veteran and they pick it up real quick,” he said. “It doesn’t take hours and hours to show someone how to operate the machine or how to actually change out the screens.”
“It’s also a lot easier to get parts than other machines we’ve dealt with in the past,” Barnes said. “With other machines, the parts all came from overseas, and we’d be down weeks at a time waiting on a simple part. That’s money we’re losing. The GT205 is American-made, and its parts are readily available, which is important to us because downtime is everything. We’ve also got faith in our partners at Stone. If we have a problem, it doesn’t matter if they’re on vacation or not, they’re readily available to pick up their phone and get the problem fixed to keep you going.”
Find Astec product availability nearby
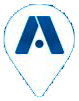