Close Quarters
Making the trek up the steep, mountainous terrain of Tillamook, Oregon, is no easy feat – especially when you’re maneuvering 111,000 pounds of solid iron and steel.
The narrow, winding logging roads and tight corners make hauling equipment a serious challenge for contractors who crush base for roads used by logging mills, timber companies and others in the forestry industry.
For Ron Braxling, owner of Braxling & Braxling, equipment size became the primary consideration when updating his old rubber tire plant. With roughly 20 jobs performed annually for the forestry industry, he needed a compact but powerful plant that would allow him to easily move from location to location, crush within a tight footprint, handle diverse types of difficult material and make a variety of products, all while meeting a stringent state spec.
“We have different needs than many contractors, as we don’t just easily pull into a quarry and start crushing,” he said. “Logging roads typically follow the outside of the hillside, and there are natural barriers and restrictions because of the culverts and streams you encounter. That poses challenges when you are trying to haul a crusher to get to the pit.”
“Not to mention, we often encounter material that is marginal,” he added. “We might process clay or stickier material – we don’t go into many environments where we consistently have good, hard basalt rock. We have to make sure to mix that material up for a high-quality, consistent end product
Braxling found his answer for a compact but high-performing crusher in the GT200CC and FT200CC, two track-mounted, closed-circuited cone plants from Johnson Crushers International (Astec).
“We were the first contractors in North America to try the GT200CC after its launch,” he said. “JCI has been so good to work with. They ask for feedback regularly and look for things to improve to better meet our needs, and work with us to implement those design changes.”
BUILT ON PASSION
Braxling & Braxling is a second-generation contracting company serving all of northwest Oregon. Started in 1961 by Ron’s father, Art, Braxling & Braxling was built on a passion for hauling materials and working in the woods. Today, the company has approximately 30 employees and is one of the leading contractors in the Oregon forestry industry.
In addition to their mobile contracting services, Braxling & Braxling also owns two commercial quarries in Newport and Tillamook. The company primarily makes road base products including ¾”, 1”, 1-1/2”, 3” and 4-6”, as well as concrete recycle material.
Braxling has spent the past three years investing in track-mounted equipment from Astec, selecting the equipment for its mobility, performance capabilities and user-friendly design.
The GT200CC uses a 1200LS Cone Crusher and is capable of producing up to 385 tons per hour. Its slightly bigger cousin, the FT200CC, is still just 12’ by 61’ ¾” long, and features a Kodiak Plus® K200+ Cone Crusher, with a capacity of up to 400 tons per hour.
Both cone plants are engineered with a unique roller bearing design that generates higher efficiencies and can reduce operating expenses by up to 50 percent, according to Stephen Whyte, product manager for track-mounted equipment for Astec.
The plants use a two-stage system that allows Braxling to meet spec, whether he’s making a ¾” or 3” product.
“Our track cones allow us to make a really broad range of products with less equipment while minimizing set-up and transport time,” Braxling said. “The ability to change the settings on the fly is really beneficial to us, and we also appreciate the remote control aspect so we can have fewer guys on the ground.”
When out on a contract crushing job, the rock is first drilled and blasted by Mccallun Rock Drilling. Braxling then builds a pad and moves his equipment in – typically an excavator, the FT2650, GT200CC and the FT3660 Track-Mounted Conveyor. Within a day, the site is set up and rock is ready to be crushed, Braxling said.
After being blasted, the material is loaded by excavator or loader into the FT2650 Jaw Crusher. The company typically uses an excavator to better control and sort the mix, Braxling said. Next, the material is run through the GT200CC Cone Crusher. Because the track plant is closed circuited, the material can be rerun to bring it to spec if needed. The material is then stockpiled using the FT3660, a 36” x 60’ Track-Mounted Radial Stacker.
“With the jaw, we can close our closed-side-setting and get down to a 3” rock, but the cone gives us the versatility to get down to a ¾”-minus,” Braxling said. “The closed circuit configuration gives us the ability to control our finished products. With an open circuit plant, you can get elongated pieces or a few stragglers that don’t meet spec. With the spec we have to meet, you have to produce a lot of fines a lot of the time, and there aren’t a lot of natural fines here. We wouldn’t be able to do this without having the closed circuit plants.”
A CLOSE COLLABORATION
Braxling & Braxling’s relationship with JCI has continued to grow in the four decades since Art Braxling first invested in an ElJay cone plant. The company also owns a FT2650 Track-Mounted Pioneer Jaw Crusher, a 2436 Pioneer Jaw Crusher and a FT3660 Track-Mounted Radial Stacker from Astec.
“We’ve carried on with JCI because of their service,” Braxling said. “For me, the true test comes after the sale. I appreciate that the equipment is made locally in Eugene and that my team has a great rapport with all of the guys at that facility – all the way from the top down. We know that every piece of equipment is going to encounter troubles at some point, but it’s how you fix the problem and how long it takes that makes the difference to us.”
Supporting an American-made company has also been a deciding factor for Braxling, who flies American flags on his jaw crushers as a patriotic gesture.
“It’s a major factor for us,” he said. “We try to steer away from overseas parts and products. We are very conscientious about choosing American-made.”
John Hereher, operations manager for Braxling & Braxling, also values the local PRO Training opportunities his team receives through Astec. The crew learned to perform its own liner changes during a service training event last year, which has saved them significant time and money.
“The training was extremely beneficial to teaching us more about the cone plants,” Hereher said. “We’ve realized how easy liner changes are to do on the Kodiak Cone Crusher. It’s an extremely user-friendly machine.”
The training also helped the crew form important relationships with the team at the factory, he said.
“Any of our guys can call down there any time they have a problem and someone will answer the phone and help troubleshoot and guide them to a solution,” Hereher said. “It’s invaluable.”
After years of collaboration, the relationships are more than just business – they’ve become friends he can count on in a moment of need, Braxling said.
Braxling recalls one memorable experience when the GT200CC went down and JCI engineering manager, Gary Heesze, l visited the site with engineer, Tom Furrer, to help troubleshoot the problem. What Braxling witnessed stays with him to this day.
“Here are two guys who are white-collar engineers with an exceptionally broad range of knowledge and mechanical ability,” Braxling said. “I finally left at 1 a.m., but these guys stayed on and were there at 6 a.m. in the pouring rain working on the equipment.”
“Their dedication and fortitude amazed me,” he continued. “For those guys in their positions to be that dedicated to stay in the muck and rain trying to solve our issues – it spoke volumes about who we were working with.”Find Astec product availability nearby
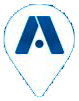