Consistency Key to Paving Airport Runways
Highlights
Country / Region | United States |
---|---|
Installation Sites | Dulles International and Andrews Airforce Base |
End User | Atlantic Contracting and Materials |
Application | Airport Paving |
Material Type | Concrete |
Equipment | RexCon Model S Concrete Plant |
Products
Most construction companies you talk to do not voluntarily sign their crews up to complete airport paving projects. It’s grueling, painstaking work that requires intensive training and permitting by your crew. Yet for Atlantic Contracting & Materials, airport paving is their specialty.
“We service anywhere from North Carolina to New Jersey along the I-95 corridor doing Department of Defense and Federal Aviation Administration work,” Seth Lillard, plant manager at Atlantic Contracting says. “Military bases and FAA government airfields are our bread and butter.”
Atlantic Contracting has extensive experience navigating the changing specifications associated with these type of projects, and knows what it takes to successfully complete them.
Mobility Matters
This year, Atlantic Contracting was busy reconstructing runways at two different airports, Dulles International and Andrews Airforce Base. In order to keep a consistent supply of mix running at both sites, Atlantic needed equipment they knew could keep up.
The company has been using RexCon Model S concrete plants since the 1970’s. They currently have 2008, 2012 and 2016 models. With the increase of work in 2020, the company purchased yet another Model S plant for the Dulles project.
“These plants are perfect for what we need,” Lillard says. “Mobilization and demobilization are extremely easy. With everything included, it’s 15 moves and you’re up in the air in one day, and running mix in three days.”
The team at Atlantic is not only comfortable with these machines, they are also pleased with the reliability of the equipment.
“The basic design of these plants has not changed over the years and each of the four plants have the same components and can be run the exact same way,” Lillard says. “The technology has gotten much better over the years, but the basic design has not changed and that’s important for our crew in providing the ease of use across each job. We know these machines in and out and are extremely comfortable with them.”
Consistent Supply of Mix
When Atlantic Contracting was chosen to work on Andrews Air Force Base and Dulles at the same time, the company knew it was time to invest in another plant.
“This year, the jobs presented themselves to where we had enough work going at once to warrant the purchase of another plant,” Lillard added. “We had two plants at Andrews Air Force Base, one on both sides of the airport, and knew we would need two plants on either side of the airport at Dulles as well.”
Atlantic Contracting was hired to reconstruct Runway 1C-19C at Dulles and needed a plant on each side of that airport to keep their paver fed, and to meet project specifications.
“Most of the specs read that you have 30 minutes from time of batch to the time of placement,” Lillard says. “With the second plant at Dulles, we were able to keep the mix production as close to the paver as possible.”
The two plants also allowed crews to keep up with the amount of mix needed to keep the project moving along.
“We pour anywhere from 12 to 22 inches deep depending on if we’re pouring a fueling apron or a runway,” Lillard adds. “It takes a lot of concrete in a short amount of time to keep these pavers happy. These Model S plants are great for feeding slipform pavers and that’s what we run for these projects.”
On the Dulles project, the plants were producing upwards of 300 cubic yards per hour for up to 12 hours each day.
“With an experienced operator that can really dial a plant in, we are able to consistently produce 300 cubic yards per hour without the shrink drum package,” Lillard says. “And if we can maintain that average all day like we have been able to, everyone is happy.”
To keep the mix moving even more efficiently, Atlantic Contracting used their own fleet of articulated trucks on site.
“We had anywhere from six to 20 off road trucks working to keep concrete in front of the paver,” Lillard adds.
The crew at Atlantic has reconstructed about 5,000 feet of runway at Dulles along with some adjacent taxiways. They began their work in March and they will turn the runway back over to Dulles November 14th.
One Family, Four Divisions
Atlantic Contracting and Material Co., Inc. is a fourth generation general contractor serving the Washington Metropolitan Area. The first generation, under R.T. Madden, started out building gravel roads in Wisconsin. They paved city streets, curbs, gutters, and progressed to highway paving. R. T. Madden's son, John, joined the business in the 1950's and became president in 1963. He expanded the business to include aggregate crushing and recycling, materials and demolition.
John Madden relocated in 1984 to the Metropolitan Washington Area renaming the company Atlantic Contracting and Material Co., Inc. and began working on many key federal and regional government projects. John’s son, Tom Madden, joined the business in 1984, became president in 2003 and expanded the business to include excavating, grading and underground utilities. John's son Michael Madden joined the company in 1992 and grandson Matt Madden in 2011.
Today, the company has nearly 100 employees operating in four different divisions.
Seamless Transition
The team at Atlantic Contracting has a long history with RexCon and their Model S plants, now owning four of them. When Astec Industries purchased RexCon in 2017, the change for Atlantic was seamless.
“I still call my same parts guys, with a couple new guys mixed in there, but everything has been the same on our end,” Seth Lillard with Atlantic Contracting says. “If I need parts, I still call my same contact in the shop. None of the major players have changed and so we’ve been very happy with that.”
Find Astec product availability nearby
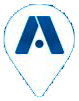