Custom-Cut
Craig Raske knows that his equipment is only as good as the people on the ground running it. That's why he makes certain his operators and supervisors are not only well-trained to run the equipment, but are heavily involved in the design and purchase of any new equipment as well.
As aggregate equipment manager for Knife River in St. Cloud, Minn., Raske is responsible for managing equipment purchases for portable operations in central Minnesota and North Dakota, where washed concrete rock is produced. Knife River is one of the top 10 largest aggregate producers in the United States and is one of only three companies on that list to be American-owned and operated. The company employs 4,800 people in 19 states and brought in $1.9 billion in revenue in 2015.
The way Raske sees it, his operator-centric philosophy is just common sense. After all, who better knows what is needed for operational success than the people running the equipment every day?
“Our operators are the bread and butter of our organization,” Raske said. “They're the people that are on the ground making us money. They run our equipment every day, and they know all of the nuances that increase production and quality. Operator feedback is really critical in our organization. We get them involved in building and designing our plants, and we do that quite often.”
With the goal of increased production in mind, Raske set out to find a portable washing and screening plant that was highly productive, portable, and most importantly, could be custom engineered to meet Knife River's needs. He found success in Astec's 1830PH portable washing and screening plant, which has increased production by nearly 30 percent and helped reduce the company's cost to its end user.
COMPLETE CUSTOMIZATION
When it came time for Raske to purchase a new portable wash plant in 2013, he turned to Road Machinery & Supplies (RMS) in Savage, Minn., an authorized Astec dealer. RMS has been Knife River's preferred supplier for the past 20 years, and Raske knew Astec could provide complete, customized aggregate washing systems that were not only highly productive, but portable as well.
Astec is the only American manufacturer that builds all of the equipment in its washing and classifying plants. In addition to washing and classifying equipment, it also manufactures full lines of crushing, screening and material handling equipment.
After comparing features, dealer support and price with several other competitive products, Raske determined that the 1830PH portable washing and screening plant from Astec was the best plant to increase production while maintaining portability. The 1830PH features a 6' x 20' triple-deck horizontal screen with 44” x 32' twin sand prep screws.
Raske had already examined the standard 1830PH plant RMS had in stock at its location in Shakopee, but knowing Astec was capable of custom engineering the plant to Knife River's exact specifications, he traveled to RMS with his operators and supervisors. Once there, he had them thoroughly inspect the plant and make a list of their wants and needs, then met with engineers from Astec and determined what modifications could be made to meet their productivity, portability and safety goals.
“We made about a dozen modifications from the factory plant to meet our specific needs,” Raske said. “The upgrades and custom modifications were something that we couldn't get from any other manufacturer. It's what set RMS and Astec apart from their competitors.”
PORTABILITY AND PRODUCTIVITY
Any plant that Knife River invested in had to be not only extremely productive, but highly portable as well. Portability is critical to the Minnesota and North Dakota divisions of the company, which do not operate out of any large deposits. The company operates primarily out of small sand and gravel pits and moves up to 10 times per year.
To improve the portability, Astec designed hinged folding flares for the 44” twin fine material washer that eliminated the need for a second transport load. Over the course of a year, this can save days in set-up and tear-down and significantly reduce transportation costs.
“Switching from 36-inch screws to 44-inch screws was important to increasing our productivity, but it also made portability a bit more challenging,” Raske said. “The fold-in flares were an integral part of the design of this wash plant. Without them, we would be unable to maintain our portability, and portability is a very essential part of our operation. With the 44-inch screws, we have been able to increase our productivity by up to 30 percent, while at the same time keeping our operation portable.”
Safety is also an essential part of Knife River's culture, and based on the recommendations of his operators and supervisors, Raske decided to add optional safety features, including roll-away screen chutes that provide access to screen cloth for increased ease of maintenance and an extended walkway.
“Maintaining equipment can be a safety challenge for our employees on site, and we are very focused on making our equipment as easy and safe to use as possible,” Raske said. “We want to make it easy for our operators to get in and out quickly and safely to do standard maintenance items like changing screen cloth. This makes their jobs easier and safer, and at the end of the day makes us a better, more productive company that can better serve our customers.”
DEPENDABLE PARTS AND SERVICE
The ability to custom engineer a portable washing and screening plant that could increase productivity and product quality was a critical factor in partnering with Astec and RMS, but parts availability, support and service were vital as well, Raske said.
“RMS and Astec have done a very good job in servicing their products,” he said. “If we're down and we need something, they do whatever they can to get us up and running as soon as possible. The service department for Astec is excellent – I can call them any time I want. I have their personal cell phone numbers, and we have solved problems at 11:30 at night when we're away from work because the service technicians are willing to answer the phone at that late hour and do whatever it takes to get us up and running.”
Find Astec product availability nearby
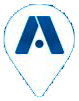