Cutting Edge Road Technology
exactly what they wanted.
Highlights
Country / Region | USA |
---|---|
Site | Lee County, Alabama |
Project | Milling NCAT Test Track |
Equipment | RX-700 Cold Planer |
Key Feature | Dual Averaging System |
Products
One of the most important places concerning the future of asphalt is in Lee County, Alabama, at the National Center for Asphalt Technology (NCAT) Pavement Test Track. It’s a 1.7-mile loop of asphalt road that is specially designed and maintained as a result of an almost 40-year-old partnership between the National Asphalt Pavement Association’s Research and Education Foundation (NAPAREF) and Auburn University.
The NCAT Pavement Test Track is broken up into forty-six sections that are funded by state Departments of Transportation (DOTs), the Federal Highway Administration (FHWA), and private sector partners with support from suppliers and manufacturers like Astec. Since its completion in 2000, it’s been essential in testing experimental pavement technologies in a safe research environment. No one has had more direct involvement than Buzz Powell, who began managing the NCAT Pavement Test Track in 1999. Buzz retired from Auburn University in 2023 and currently serves as the Technical Director for the Asphalt Pavement Alliance (APA), but he still provides part-time support for his passion project to the current NCAT team.
“The whole objective is to build test pavements and then run a fleet of trucks over them to tear the pavements up so NCAT can help agencies make informed decisions regarding mix and materials, structural pavement design, and pavement preservation,” said Powell.
Every three years the track is rebuilt, and this year marks the beginning of the ninth research cycle. Just like on public roadways, the milling work is phased into sections so that others may stay open for use.
“NCAT usually rebuilds about a third of the track and then does traffic continuation on the other two thirds,” explained Powell. “This cycle, however, it was a little bit more than a third, so it was quite a bit of work. Usually, the thickness of the milling varies from as shallow as three quarters of an inch to as deep as a little more than a foot.”
But this year the milling work went far beyond those typical ranges, digging down to layers as deep as five feet, as well as milling twenty-one of the tracks forty-six sections.
“They removed a tremendous amount of material,” said Powell, referring to the team at Astec and their RX-700. “What was different about the milling work this time was that NCAT asked [Astec] if they would precisely target the prescribed average depths for each section while maintaining as much smoothness as possible. It’s easy to do one or the other, but it’s a challenge to do both. This was necessary because smooth milling would help NCAT later pave the smoothest possible test sections.”
The Astec milling team knew just how to give the new team at the NCAT Pavement Test Track exactly what they wanted.
“Not every test track section was getting milled at the same depth, but they were all focused on rideability,” said Tom Lenger, Product Manager, Road Recycling at Astec. “In order to achieve that, we decided to use the Dual Averaging Sensors (DAS).”
While traditional milling end-gates only monitor about an eight-foot length of work, the DAS can expand that monitoring window up to thirty feet long. The grading system then averages the grade depth over that much longer span, generating an incredibly smooth foundation for the pavements above it.
“Normally, if you hit a bump in the road, your mill is going to immediately correct because you're within that eight-foot window, whereas with this system you're looking at the front of the machine, the middle of the machine, and the rear of the machine all at once,” explained Lenger. “You're not going to have as drastic changes in elevation on your road.”
The DAS system averages the cutting depth over the entire length of the ski, which translates into fewer and less abrupt changes in the mat. Any profile corrections made in this manner are done so not only with more precision, but at a more gradual rate of change. This, in turn, makes the eventual work of the paving team much easier.
“The grade control system and the milling quality were both outstanding,” said Powell. “It was just good work all the way around. I believe it was a step up compared to work done in the past. If you mill smooth, it’s easier to pave smooth. Smooth test sections are essential to good research”
NCAT will begin monitoring performance data after track reconstruction is complete. Employing technology like the Dual Averaging Sensor system can have a direct impact on the final result.
“Up until now, the data for environmental product declarations (EPDs) has stopped at the plant gate, but soon data will be pushed out to the job site,” said Powell. “When you run a milling machine and hit your target on the very first pass using precision control systems, you don’t have to do extra work to correct deficiencies. Because corrective work or additional machine passes are not required, the result will be less machine hours and a lower embodied carbon roadway. Smoother roads will be even more important in lowering carbon footprint when the use phase is eventually considered.”
However, there were some sections that needed to go much deeper, getting down far enough into the subgrade material that NCAT could complete the removal with a bulldozer for a special new experiment.
“Most test sections at the NCAT Pavement Test Track are built on local subgrade that’s very high quality and great for experiment control. When this is done, performance on the surface is not confounded by foundation differences. Sometimes, long hauling different subgrade from another state is essential to the research,” said Powell. “With this particular deep mill section, NCAT needed to build the section on a subgrade that is common in the State of Mississippi.”
Why would engineers at the NCAT Pavement Test Track want to remove the good material and replace it with lower quality subgrade? The objective of the experiment is to compare an existing section built with conventional cement stabilization to a new section built with innovative cement replacement technology.
“NCAT is evaluating a new technology that potentially allows you to slash the cement content and stabilize layers through the use of an environmentally sustainable enzyme,” said Powell. “It’s a lower embodied carbon approach to doing stabilization. That was the reason for milling the deep section.”
Even at depths in excess of thirty inches, the RX-700 took care of business. For these depths, the DAS ski system was removed, and the team set to work removing the material in lifts of about ten inches per pass. The machine is capable of cutting depths up to fourteen inches and comes available in cutting widths from 6’ 7” all the way up to 10’ wide.
“We did three ten-inch lifts with the RX-700, and it wasn't all asphalt, there was a lot of sub layer that we were taking out as well,” added Lenger. “The whole job took about a week to complete, but there were so many different situations that we saw in that condensed amount of time that, in normal situations, a contractor might only see once in a great while. We were meeting a different challenge every single day.”
The heavy-duty RX-700 features an 800 horsepower engine and was more than capable of tackling whatever the NCAT Pavement Test Track could throw at it.
“It was a really unique experience,” said Lenger. “We really value what NCAT does. In our industry, there's academia, there's manufacturers, there's producers and customers, and we really value what NCAT does for the industry. That's why we wanted to be involved in helping them rebuild their test track.”
“It was just good work all the way around,” concluded Powell. “Of course, the Astec team is always great to work with, and they've been a blessing to us through the years. It would not be possible to continue to do game changing research at the NCAT Pavement Test Track without this type of support from great industry partners.”
Find Astec product availability nearby
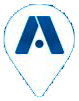