Doubling Production
Con-Agg Companies, a leading supplier in crushed limestone, concrete products, andwarehousing is producing more tons per hour and increasing efficiency with their newTelsmith 8×20 and 6×20 Vibro-King TL® Portable Screen Plants, Titan™ T400 PortableCone Plant, and TRAC10® Automation System.
Con-Agg Companies operates more than 50 aggregate and ready-mixed concreteoperations across central and northwest Missouri and central and northeast Arkansas.
On the aggregate side specifically, Con-Agg operates under a few different names- BooneQuarries, Norris Quarries, and Mid-Missouri Limestone – producing concrete and asphaltaggregate, base products, clean aggregates, road rock, riprap, and agriculture lime.
A division of Summit Materials, Con-Agg has more than 500 employees serving a largegeographical footprint, which provides unique opportunities, but also challenges. Oneregular challenge is meeting production requirements, but part of overcoming this hurdle isregularly assessing and modernizing equipment.
Ronnie Simms, Quarry Manager of Con-Agg Companies is in charge of the Mid-MissouriLimestone Auxvasse South Quarry in Auxvausse, MO, along with 16 other quarries inMissouri. This location is processing concrete rock that goes into their precast and concrete plants.
However, as a 37-year veteran if the industry, Simms recognized the Auxvausse SouthQuarry needed upgrades. "Our old stationary plant included worn-out equipment that wasno longer dependable or producing to our needs," says Simms.
SOLICITING SOLUTIONS
With the old plant at the Auxvausse South Quarry producing only 200 tph, Simms contacted Jerry Hall, regional sales manager at Telsmith, to see how Telsmith could assist the operation. Con-Agg's first experience with Telsmith came in 1997 when it purchased a full modular plant that is still running today for the Boone Quarries West operation. "We have been running Telsmith equipment for 22 years, so the decision was clear to choose Telsmith again," Simms says.
The timing was perfect, as Telsmith had an 8×20 Vibro King TL® Portable Screen Plant and a Titan™ T400 Portable Cone Plant in stock, ready to ship. From there, Con-Agg abandoned it's 50-year-old stationary plant and moved its new portable plants to a better location within that quarry. Con-Agg went from primarily impact crushing to compression crushing as their old plant had a primary jaw crusher and secondary impact crushers.
In addition to the 8-ft. x 20-ft. Vibro-King TL and the Titan T400, Con-Agg introduced a 6-ft x 20-ft Vibro-King TL portable screen plant to the operation as well as Telsmith's TRAC10 automation. According to Con-Agg, the equipment and technology makes the Auzvausse South Quarry a more efficient producer. "With Telsmith's automation system, they were able to link some of our old pieces of equipment into the automation plan," Simms says. "We put laser level sensors over our secondary crusher, tying it back to our Syntron feeder, then put a level sensor on the bin interlocking it back to our grizzly feeder. This balanced out the plant and increased our production. Telsmith's automation technology has helped us be the most efficient we've ever been. So efficient that we went from 200 TPH to over 400 TPH."
EQUIPMENT OPTIMIZATION
The TRAC10 automation on the Titan T400 cone crusher particularly impresses Con-Agg. The TRAC10® monitors crusher operations, provides automated calibration and setting controls, and protects the crusher from overload; all to yield greater crushing performance and efficiency. Operators can initiate an automated calibration process via the touch screen monitor, that automatically "zero's-out" and resets to the proper setting. Operators can also modify the crusher setting at any time, even while crushing.
"We really like the simplicity and safety aspect with the ability to service the cone from the top," Simms says. Titan™ Cone Crushers are built so the components are removed from the top instead of the bottom, reducing the need to work under the crusher, which is safer and more efficient. The main shaft on the Titan™ series cones is fixed into the lower mainframe and the countershaft sits below the main gear allowing all other components to be removed through the top.
"We currently run it five days a week at ten hours per day," Simms says. "At the end of each shift, we inspect the plant for any problems that may shut us down the next day and perform regular maintenance, which is the key to our uptime success."
WHAT'S NEXT
Looking ahead, Con-Agg plans to expand and is always looking for new opportunities to grow. "Our next step is to add a high-frequency screen in to make an asphalt fraction and our concrete rock at the same time," Simms says.
Request More Info
Find Astec product availability nearby
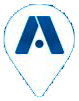