Green Initiatives Serve Communities and the Bottom Line
Shelby Materials customizes an Astec Industries BMH Central Mix Plant to meet the demands of an up and coming community in a sustainable way
Highlights
Shelby’s New Astec BMH Central Mix Plant At A Glance
The central mix plan chosen by Shelby for their new Franklin location was fully customized by both the Shelby team and Astec to meet their specific needs. With the industry demanding more green initiatives, this plant covers those needs as well. Some of the clean air and energy efficiency highlights of this plant include a gravity feed aggregate and cement discharge, on-demand water heating system and central dust collection system.
Full install details include:
- Fully enclosed with insulated panels
- Gravity feed aggregate and cement
- On-Demand aggregate heating system
- Double feed aggregate handling system (36 inch wide belts, 750 ton/hour)
- Aggregate storage bins (370 ton capacity, 6 compartments)
- Aggregate weigh hopper (12 yard, 40,000 lb capacity)
- Cement storage bins ( 480 ton capacity, 6 compartments)
- Rollmaster drum mixer (12 yard capacity, 1 inch thick with urethane liners)
- Bolt-in liners for aggregate loading hoppers and aggregate storage bins
- 304 Stainless steel water holding hoppers
- Central dust collection system
Products
Investing in equipment that not only helps you meet production goals, but also contributes to your company's Environmental Health & Safety initiatives, is a trend that will continue to grow in the construction industry.
Governments and communities increasingly expect businesses to support broader goals, such as sustainability, and construction business owners need to be ready to step up in order to stand out.
Shelby Materials, a ready mix concrete and aggregate material supplier throughout Greater Indianapolis and Central Indiana, knows the importance of differentiating your business in a particularly competitive market.
“Shelby Materials began as a small town company and we are still family-owned and operated,” Matt Haehl, President of Shelby Materials says. “We’ve grown to 10 different locations throughout Central Indiana and we remain committed to the cities and towns in which we work and sustainability is part of that.”
Shelby has been giving back to their communities for years and works hard to be a good neighbor in each location. When they sought to open their newest location in Franklin, IN, they designed the plant with that in mind
“We take pride in being a good neighbor and we are a good community partner,” Haehl says. “We want our facilities to reflect that. To operate sustainably and to look clean and professional.”
The company has 10 plant locations and purchased its first BMH Astec plant six years ago. They knew the Franklin plant would be a BMH system as well, but wanted to add new features that would allow them to accomplish both their community and environmental goals. And they started from the ground up.
Green Site Prep
Before the new plant was installed, Shelby used their crews and equipment to prepare the site. They brought in reclaimers and used a relatively new material, Liquid Fly Ash, when constructing the paved areas.
“We used the Liquid Fly Ash to lower our cement content in all our paving around that plant, which was about 6,000 yards of pavement,” Haehl says. “We were also able to use an admixture product to help reduce the cement content, which saved about 100 tons of carbon reduction.”
By doing this, Shelby did not have to use sealers on the concrete which was an additional way for them to lower their environmental impact.
“We saved 800 gallons of using sealer, which is a lot of plastic buckets saved,” Haehl adds. “That was pretty beneficial to the project and our goals.”
In the mix, Shelby also used a Type 1L Cement, which further helps with carbon reduction.
“With 1L Cement, they put in a little more limestone in there, and they can reduce the carbon,” Haehl says. “By using that product, it was another 68 tons of carbon reduction that we were able to do on this project alone.”
Shelby had used the Liquid Fly Ash and 1L Cement before, but wanted to get more comfortable with the material before rolling it out to other customers.
“This project at our location allowed us to gather quite a bit of data for ourselves and our mixes,” Haehl says. “But it also helped us generate some information for future use on other projects.”
Installing a Sustainable Plant
And Shelby is keen on relying on their past experience, especially when making a new purchase. They contacted their BMH salesman at Astec to get the ball rolling with their new Franklin location.
“We had a great relationship with BMH for years and this being our third permanent BMH plant, but first under the Astec umbrella,” Haehl says. “We bought our first BMH six years ago and decided to continue with this trusted brand for the new location. We had an idea of what we want to work with in Franklin and the Astec team are the professionals in the plant construction business so they took our ideas and made suggestions for the location and ran with it.”
The first suggestion that Shelby incorporated was insulated panels for the plant which helped with install time and their goal of being a good neighbor.
“Normally when you build your plant, you have to build a building around it,” Haehl says. “Astec installed the insulated panels when they installed the plant which saved a lot of time during install. This made it easier to move forward faster, and also is more aesthetically pleasing for the neighbors. This is definitely a better-looking plant.”
The fully enclosed panels help with heat retention at the plant as well, making this the first of many green systems installed at this location.
Another feature that helps save time and money is the gravity-fed system installed here.
“This system allows the aggregates and cement to fall instead of being pushed with a conveyor,” Grant Harman, Plant Maintenance Manager at Shelby says. “Now we have less conveyors, so we’re using less energy and that’s where the savings come into place there. Also, we save money on belting since we don't have the wear and tear on conveyor components.”
That makes the gravity feed system beneficial from a maintenance standpoint as well.
“We have basically eliminated components that many manufacturing facilities have problems with,” Harman says. “You get rid of gearboxes, you get rid of pulleys, belts, things like that. With this plant, we have six cement silos, six aggregates and we don't have to worry about any of the conveying systems. With this system, you don't have the energy with the motors, you don't have your problems with gearboxes, and you also don't have any conveyor components to worry about.”
Down With Dust
Dust control has been a big focus point for plant manufacturers over the years and Shelby made it a priority by installing new solutions in Franklin that keep this issue under control.
“Dust collection at any plant location is twofold,” Haehl says. “It's a necessity for us as far as keeping dust under control for maintenance and things of that nature, but it also is a benefit to our neighbors. Less dust keeps our buildings clean and our people safe.”
The central dust collection system installed in Franklin is another state-of-the-art component that keeps Shelby workers safe and equipment clean all while helping them be good neighbors at the same time.
“The way that this dust collection system operates in this plant, people aren't really going to see what goes on outside of the building, which is the point,” Harman says. “Inside the building, it doesn't just do dust collection from the mixer side, it does dust collection from the dry side as well.”
Loading any dry material creates a lot of dust inside the plant and it can get inside components and cause issues if not properly contained.
“To counteract this, we have ducting running into just above our aggregate bin and also right near our cement bin,” Harman says. “The dust collection systems inside have been working really well.”
Outside the plant, Shelby is using an automatic pressure system to counteract dust which saves on energy and component wear.
“Our dust collection system used to just be set on timers and they would just kick on for 45 seconds every two to three minutes,” Harman says. “After a while, that high pressure pulse would end up destroying the pleating inside of the filters and seven of those filters ends up being about $1,700 for us and we're going through that several times a year.
“Depending on how many silos you've got, seven filters per silo on these units adds up,” Harman says. “With the on-demand pressure system, there are less filters but we also have a flow control system or a pressurized system that’s going to cut down on our costs for our filters and maintenance in general as the system only works when it needs to.”
On-Demand Heating
The most expensive part of any plant operation is heat. Drying aggregates requires heat and that energy usage adds up quickly. Plant owners can counteract those prices by using on-demand heating systems.
“In the past, we used sand heaters to heat our aggregates which allows for a better product in the wintertime,” Haehl says. “This obviously uses a lot of gas to operate so we were seeking a better solution.”
Shelby installed a Polarmatic System which uses the heat much more efficiently.
“When we’re heating materials, we’re going to be using all that gas and everything to heat our water anyhow,” Harman says. “With the Polarmatic, instead of just having the flue gasses or the heat exhaust into the atmosphere, we redirect that to each and every ag bin. We have valves that will turn on or turn off depending on how often we want to put that heat into each individual aggregate, whether it's the course or the fine. So essentially, we're utilizing something that we already had to give us a better quality of a product.”
Shelby was able to eliminate the need for a sand heater at this location and now heats their aggregate as they heat their water with the Polarmatic system which gives them cost savings in many areas.
“In our other locations, we have burners heating the aggregates at 10 million btu and we eliminated that here,” Haehl says. “We also are not heating more sand than we need and we don’t require a loader to shuffle materials back and forth to the heater so there are further energy and fuel savings as well.”
Consistent Support At Every Step
Customizing a plant to meet your needs is a great way to serve your business, but it can be frustrating if you have the wrong partner.
“We knew what we wanted, but we also knew we needed to work with a trusted partner to execute,” Haehl says. “With the first two BMH plants we put up, we had a good relationship with Astec. They were really easy to work with and this new install was no different. If we had a question, we got some quick turnaround service and they would send someone onsite pretty quickly to diagnose any issues and help the project move forward.
“With the BMH Astec transition, service has never been better,” Haehl continues. “Now that service is stateside, they're pretty close to us if we need anything and it’s really been a pretty easy transition.”
New systems often come with learning curves and Astec staff is also available to help with training and any ongoing support that is needed.
“Anytime you get a new component or new piece of equipment, whatever it may be, books just don't give you all the answers,” Harman says. “We are very fortunate that Astec has a good group of people that have been doing this for a long time. We’ve developed a great relationship and I’m able to contact their staff after hours if I need to. Their people are more than willing to jump through hoops to help me in any situation.”
And the partnership with Astec and Shelby will continue for years to come as they navigate a sustainable roadmap for the future together.
“Sustainability is always something we think about,” Haehl concludes. “It's something that's pretty important, and is becoming obviously more of an industry concern so it's something we pay close attention to and apply to everything we’re doing and it’s something Astec is paying attention to as well. We're very pleased with the plants. We're very pleased with the construction and the service and hopefully we're able to grow and continue the relationship.”
Find Astec product availability nearby
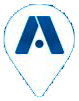