In Good Faith
When you're the largest concrete producer in Peru, there's no room for error in equipment purchases. That's why when Leslie Orams decided to buck traditional methods of producing manufactured sand and try a roller bearing cone crusher in place of a vertical shaft impactor (VSI), he knew how important extensive testing would be in the purchase process.
"I needed to have confidence that I was going to keep my job once the plant began to work in the project," said Orams, general manager of all quarries for UNICON, the largest ready-mix corporation in Peru. "Because purchasing the equipment was an act of faith, I decided to make my own series of tests to assess the crusher's capabilities and conduct my own sieve analysis of the products."
After documenting the results through a series of tests that proved what the AggFlow simulations projected, Orams discovered that not only did the cone crusher increase capacity by 25 percent while still making the same-quality product as a VSI, but it also allowed the company to increase their ratio of a higher-demand product.
AN INNOVATIVE PROPOSAL
UNICON is the largest ready-mix producer in Peru, and its Lima quarry is also the largest in the country, producing approximately 3.6 million tons of aggregate per year. The company dominates with nearly 75 percent market share in Peru, and is aligned with UNACEM, the largest cement producer in Peru. UNICON also operates in many of Peru's leading mines.
Orams, who oversees aggregate production operations for UNICON, and Paul Huayta, General Manager, Equipment Maintenance and Quarries, first began considering alternative methods of manufacturing sand when a large-scale mining project in Las Bambas required more sand than their quarries could produce.
Orams was already familiar with the quality of machines manufactured by Astec Industries. In 2008, he observed one of the corporation's cone crushers running in Córdoba, and was impressed by the stillness, and no vibration, of the plant as it operated. Soon after that, he learned of the use of KPI-JCI and Astec Mobile Screens equipment, for another operation in Panama, and became more intrigued by the company's products.
KPI-JCI and Astec Mobile Screens is a premier manufacturer of heavy equipment for the aggregate, recycle, construction and mining industries. The company is part of the Astec Industries family and manufactures a full line of crushing, screening, material handling, washing and classifying, stationary, mobile and portable equipment.
Prior to the Las Bambas Project, UNICON had never needed to manufacture sand, since natural sand accounts for nearly half of the aggregates produced in its quarries. Using a cone crusher to manufacture sand wasn't even a consideration for Orams, until it was suggested to him.
"VSI's are strongly positioned in the market of sand manufacturers," Orams said. "If you ask any contractor the best way to produce sand, a VSI is almost always the answer. I didn't even know sand could be produced using a cone crusher until it was recommended to me."
PASSING THE TEST
Seeking a better and more efficient solution for sand production, UNICON began considering the products developed by Astec Industries companies, and finally selected KPI-JCI and Astec Mobile Screens' Kodiak® Plus K200+ Cone Crusher.
The K200+ is a 200-horsepower cone crusher and one of four models in the Kodiak Plus family of products. The K200+ features a precision roller bearing design, as well as a new hybrid cast/ fabricated base frame design, the ‘MILO' automated control system, a new patented liner retention system, patented thread locking ring and anti-spin cone brake. Other features of the Kodiak Plus product line include patented replaceable brass thread inserts, patented internal counterweights, a heavy-duty tramp iron relief system consisting of pressure-relief valves in lieu of accumulators, and brass v-seat liners.
Prior to his introduction to the roller bearing design of the Kodiak Plus Cone Crusher, Orams had only used bushing cone crushers, but now Orams says he will "never go back" to the bushing design.
"In the past, I thought roller bearings could cause more issues, but once you use a Kodiak, you will never stop using it," he said. "Working with roller bearings gives you a greater level of accuracy, your settings are perfect, your products are better and you have a greater loading capacity. If an internal problem occurs, such as non-crushable material getting through, the risk of internal damage is less than using a bushing, because a bushing gets crushed; in the case of a roller bearing, you just have to change it. Therefore, the equipment is sturdier. This cone crusher is a very powerful piece of equipment."
Before purchasing the cone crusher, Orams ran AggFlow simulations for both a well-known competitive brand of VSIs and the Kodiak Plus Cone Crusher. Theoretically, AggFlow calculated that the competitive VSI could achieve 30 percent crushed sand, whereas the Kodiak Plus Cone Crusher, set to a 10 mm (3/8") closed-side-setting (CSS), could produce 64 percent crushed sand.
With this knowledge in hand, UNICON took the cone crusher to its quarry in Quijamarca for a weeklong test. The test material consisted of very hard aggregate. At a 6 mm (1/4") closed-side-setting and feeding material approximately 1 ½" and ¾" in size, the company was able to achieve 80 percent sand production using the Kodiak Plus Cone Crusher – an increase of over 15 percent compared to the AggFlow projection.
Determined to be thorough in his experiment, Orams tested the performance of the crusher at different settings to ensure the crusher could handle the capacity and the product would be comparable to what AggFlow estimated. The results of the tests proved to be "spectacular," Orams said.
"One thing that really stood out for us after testing the production of sand by using the cone was that the actual curves and ratios of the products matched almost exactly the theoretical ones shown in the brochure," he said. "It's not often that you find this in other machines – that is why they are called theoretical references – but the Kodiak proves true every time. When I factor in the AggFlow when working with other brands, I usually plan for 60 percent capacity of the equipment. With the Kodiak Plus, I plan for 90 percent of the capacity, because I know the output is going to match the specifications. It is very reliable."
After the initial tests, Orams began a second round of testing, this time replacing UNICON's old cone crusher at its Quijamarca quarry, which had reached the limit of its capacity and no longer satisfied UNICON's demands for higher production of a certain specification.
"We needed more of the ¼"-¾" product, which was higher in demand, but we were producing excessive amounts of ¾" to 1" product," Orams said. "By this time, we knew that the Kodiak Plus cones were reliable enough to reach the claimed production. Therefore, we replaced the existing bushing cone with a Kodiak Plus cone, with the aim of having a better balance of loads, and with the hope of increasing production."
The result of replacing one 200-horsepower bushing cone crusher with a Kodiak Plus K200+ Cone Crusher led to a 30 percent increase in production capacity, Orams said. With the increase in production, UNICON was able to change the ratio of products, thus increasing the production of its highdemand product (¼"-¾") from 50 percent to 70 percent. This was all accomplished without increasing the amount of man hours, a necessity because the company was already operating 24 hours a day.
With increased confidence in KPI-JCI and Astec Mobile Screens, UNICON moved forward with installing a complete system at Las Bambas, a premier copper mine in the Cotabambas, Apurimac region of Peru. UNICON produced 100 percent of its crushed sand product at the Las Bambas mine using its new Kodiak Plus K200+ Cone Crusher, which is used for construction and development of the mine site.
Thanks to the complete system of KPI-JCI and Astec Mobile Screens equipment, when UNICON faced an additional challenge of a water shortage on the Las Bambas mine site, it was able to pair its new cone crusher with a KPI-JCI and Astec Mobile Screens high frequency screen to produce the sand without water.
The high frequency screen is known for its aggressive vibration that is applied directly to the screen, which allows for the highest capacity in the market for removal of fine material – including dry manufactured sand.
"Traditionally, when you are trying to reduce the fines of a product, you use a wash plant to wash the fine material away," said Patrick Reaver, product manager for KPI-JCI and Astec Mobile Screens. "However, the high frequency screen allows you to screen very fine material, and in some cases, depending on the moisture content of the product, a high frequency screen even eliminate the need for washing the product."
"This solution was critical for the success we've had at the Las Bambas mine," Huayta said. "If we had not offered that solution, the project would not have been feasible,because the water is such a scarce resource. Therefore, the ability to produce aggregates without water out to be a very important advantage for this project."
A BRIGHT FUTURE
Today, UNICON owns an extensive spread of KPI-JCI and Astec Mobile Screens equipment, including four Kodiak Plus K200+ Cone Crushers, three 7203LPPM horizontal screens, 16 stackers, one CS5260 horizontal shaft impactor and multiple AMS high frequency screens.
Beyond the production capabilities of the equipment, Orams and Huayta also highly value the support from the authorized dealer INTERMAQ S. A. C. in Peru, as well as the three manufacturing facilities, located in South Dakota, Oregon and Illinois in the United States.
"We appreciate that when we call the factory, they are ready to answer," Orams said. "They offer 24/7 service, which makes the customer service very good. Post-sales support from the dealer and manufacturer is a very important variable to us when purchasing equipment. It is as important to us as the price of the equipment."
Huayta said it was his experience visiting the manufacturing facility and speaking with the experts on ways to custom engineer the equipment to meet the company's unique needs, that led to the final sale of the equipment.
"The factory was very receptive and willing to adapt to our local needs," Huayta said. "For example, the horizontal screens are normally mounted on very large frames, which are not useful in Peru. Upon request, the factory mounted the screens on shorter frames, which allowed them to be very maneuverable and gives us all the versatility we need."
Despite a small decrease in the growth of Peru's economy in 2014, Huayta expects a surge in infrastructure projects in Peru in 2015 and beyond, in which UNICON plans to play a major part.
"Our aim is to be present in all of the large mining projects and in all of the large mines, producing those particular elements that not many companies produce, such as material for dams or structural fills," Huayta said. "As the natural reserves of sand begin to deplete, we know it's going to be very important for companies to learn to produce sand in an efficient manner. We foresee that this is going to be the great problem in the future, so we want to be one step ahead of the problem today. And we believe we are definitely increasing our opportunities for the present and the future by using cutting-edge equipment."
Request More Info
Find Astec product availability nearby
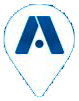