Investing In Independence
Entering the asphalt recycling market is no easy feat, even for the most experienced producers. But for Ajax Paving Industries of Florida, LLC, processing its own recycled asphalt materials led to a savings of up to 50 percent, along with the ability to produce a higher-quality product, increase the amount of recycled product in its mix, and eliminate its dependence on sub-contractors.
Since opening its first asphalt plant in Detroit in 1961, Ajax Paving Industries has become an industry leader and the number one asphalt company in southeastern Michigan and Florida's Gulf Coast. Today, the family-owned company operates seven asphalt plants in Florida, and produces approximately 1.5 million tons of hot-mix asphalt.
Recently, Ajax invested in a mobile crushing and screening spread, which allows the company to process recycled asphalt pavement (RAP) when and where it needs it, according to Vince Hafeli, vice president of plants and materials for AJAX in Florida. The company anticipates producing between 500,000 to 600,000 tons of RAP in 2016.
"Processing RAP in Florida is critical," Hafeli said. "All producers process RAP and all producers need a high quantity of RAP to be competitive and to get work in this state."
Although Ajax first began considering the idea of investing in a mobile crushing and screening spread to process its own RAP material more than eight years ago, it wasn't until 2015 that the company took the next step and purchased an FT4250 impact crusher, GT205S screen and 13-3080 80-foot conveyor from KPI-JCI and Astec Mobile Screens, sold through Flagler Construction Equipment.
The FT4250 track-mounted impactor plant is part of the exclusive continuous crushing and tracking impactor family. Featuring an Andreas Series Impact Crusher, the FT4250 delivers up to 25 percent more production and up to 30 percent more uptime than competitive models. The GT205S is a track-mounted screening plant that features a low-profile and compact design for easy access to all controls for set-up.
The company uses the FT4250 in an open-circuit configuration along with the GT205S and 13-3080 conveyor. The process starts with the broken-up asphalt pavement entering the impactor, where it is crushed then fed to the screen's feed hopper. From there, it is screened to a ½"- finished product. Any overs – typically 7-10 percent of the original material – are fed from the middle-deck screen back to the impactor, where it is crushed again to make a finished product. The ½" finished product is then conveyed and stockpiled to be added to the asphalt plant.
EXCEEDING EXPECTATIONS
Before processing its own RAP material, Ajax relied solely on sub-contractors to crush its material. After careful consideration, the company determined it could crush the same material for at least the same cost, if not cheaper, than what it was contracting out. Production was key, as Ajax had to be able to beat the sub-contractors' production and expense numbersto make the venture work.
Already familiar with the Astec Industries family of companies through its asphalt plants, Hafeli felt confident enough in the company's products to consider equipment from KPI-JCI and Astec Mobile Screens. Hafeli worked hand-in-hand with regional sales manager Chris Worley, who spent several years educating him on the benefits and process of creating a RAP product.
"Chris was very thorough in educating me and working through the process, and he wasn't pushy – he allowed us to make the decision in our own time," Hafeli said. "It was important to me to buy American, and we think of Astec like family, so it was a natural fit for us to consider equipment from KPI-JCI and Astec Mobile Screens."
In order for the equipment to meet the company's production goals, the crusher had to be capable of processing between 200 to 225 tons per hour of RAP, Hafeli said. Ajax is currently permitted to produce up to 300 tons per hour in Florida. Initially, Ajax anticipated it would be able to process 60 percent of the material it uses annually, but now the company forecasts it will be able to process upward of 80 percent because it is able to achieve more production from the equipment than it originally estimated.
"Everything we were told the equipment would do has been exceeded," Hafeli said. "There were no shallow promises made. We're running at an average of 290 tons per hour, and when we've experimented, we've found we could produce up to 450 tons per hour. So the equipment has greatly exceeded what they told us it would be able to do."
Meeting a production metric was only one factor in the decision-making process, Hafeli said. The equipment had to be highly mobile, as Ajax's job sites tend to be located in tight, urban spaces. The company also sought a manufacturer that could serve as a singlesource provider for all their equipment needs.
"When we began looking for a track-mounted screen to go with our impact crusher, the GT205S was an easy choice," Hafeli said. "With other manufacturers that we looked at, we could buy a crusher from them, but the conveyors and screen plants didn't come from them. We wanted a one-stop shop, so if we had an issue, there was only one company to deal with."
SIGNIFICANT SAVINGS
Once convinced of the equipment's capabilities, it was time to test it out in the field. While Ajax initially only hoped to break even – which would allow them to become independent of sub-contractors and control the quality and quantity of the material – it soon realized it was achieving a significant cost savings of up to 50 percent of what it was paying subcontractors.
The company also discovered it was able to increase the amount of RAP used in its mix by an additional five percent, which Hafeli said adds up to enormous annual savings. The asphalt pavement processed in the Gulf Coast is composed of Florida limestone, Canadian granite and hard limestone imported from various islands. Florida limestone materials tend to be high in fines content, creating additional challenges when processing RAP, Hafeli said. Ajax currently makes a ½"-minus RAP product that meets Florida Department of Transportation specs.
"By operating our own equipment, we're able to experiment and do things that we traditionally have not been able to get a sub-contractor to do for us," Hafeli said. "For example, some of the materials that we process are high in fines content and dust. We've been able to experiment with screens and change processes a little bit to allow us to process the RAP differently, which allows us to get a larger quantity of RAP into our mix. So not only is there a cost savings on the processing side, but we're able to achieve a cost savings on the production side as well."
Another unforeseen benefit has been the stronger relationships formed between the various production areas within the company.
"As strange as this sounds, the process of getting into crushing RAP has forced us to up our game, and improve our quality as well," he said. "Before, when independent sub-contractors came in, they did their thing, and we took what they gave us and we made it work."
"But now, by owning our own equipment, it has forced our quality control team, our plant foreman of the asphalt plants and the foreman of the crushing operation to work more closely together as a team. And that has led to a better product for our customers and a more successful company as a whole."
Find Astec product availability nearby
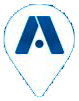