Is an electric process heater the right choice?
Application
For most applications that use heat as part of the manufacturing process, either an electric or fired heater can be used for the same process. Some applications, such as in the chemical and food industries, require an extremely accurate and constant temperature. Even slight variances can spoil the product. Either electric or fired heaters can maintain precise temperature control over these processes when equipped with accurate, high-quality measurement instrumentation and controllers.
An electric heater does have one advantage over its fired counterpart; turndown ratio. Electric heaters have unlimited range of turndown (1:100 ratio), whereas fired heaters are much more limited (typically 1:10 ratio). In most cases, it’s not a problem, but if your system has major variances in flow rate, an electric heater might be a better option. Fired heaters must be designed for a specific flow rate range and if the flow rate goes lower than a certain point the heater coils can be damaged because proper heat transfer doesn’t occur. That’s not to say designers don’t have to consider flow with electric heaters. If you modulate flow, the energy output will also need to be modulated in the same proportion for either system.
Electric or fired heater systems must be engineered to prevent damage from lack of flow. For instance, you could have a dedicated circulation pump that only circulates heat transfer fluid through the heater coil assuring that proper flow is always flowing through the heater coils. Additional take-off pumps (side pumps) pull hot liquid from the heater loop and circulate the fluid to the end-users. But this works mainly with an indirect heating process where a heat transfer fluid is being used, not a direct heating process. In addition, input modulation controllers and limit temperature switches must be installed to assure the proper operation and safety of any heater.
Environmental Impact
There is a push from experts, governing bodies, and the general population for individuals and corporations to reduce our impact on climate change. It’s important to continue to develop technologies that are more efficient and more environmentally friendly. Electric heaters produce virtually zero emissions and have 99% thermal efficiency during operation, whereas fired heaters typically have around 85% thermal efficiencies in their standard configurations. Fired heaters can be configured with additional equipment to further reduce emissions, such as economizers, air pre-heaters, and special burners.
Operation is only part of the overall equation when we talk about emissions. We also have to factor in the source of electric power. In the United States, depending on the region, fossil fuels, particularly natural gas, are still the most common fuel source for generating electricity at about 60% (natural gas 40%, coal 19%, petroleum 1%). Renewables make up about 20% and nuclear the last 20%. Power generation plants using coal have especially bad reputations as being environmentally unfriendly and are becoming less common, some converting to natural gas. In recent years, natural gas and nuclear have overtaken coal as the most common fuel sources for power generation according to the U.S. Energy Information Agency (EIA).
Although electric heaters do not generate harmful emissions, they are heavy consumers of electricity. Power generation plants that use natural gas, coal, or petroleum do produce harmful emissions which contribute to the overall impact an electric heater can have on the environment. If you live in a region that mostly uses hydro, wind, solar or nuclear, the overall impact is greatly reduced.
With fired heaters, again you have to factor in the source of the fuel. The equipment used to mine fossil fuels release emissions into the air and add to the overall impact of the heater on the environment. Natural gas power plants are considered more friendly because gas burns cleaner than coal or petroleum. There are also a number of methods and technologies that can help reduce a fired heater’s impact, from low NOx burners to waste heat recovery options. These technologies can greatly reduce the emissions emitted from fired heaters.
Overall, an electric heater is going to be more environmentally friendly than a fired heater, even when factoring in the emissions produced by power plants to power the electric heater. But it’s not by as much as you would think.
Cost of operation
While it’s important to reduce our carbon footprint as much as possible, it’s also important to do what is financially prudent for our businesses. For now, natural gas is a significantly cheaper energy source than electricity. Proportionally, the greater the heat demand for your application the more cost-effective it is to operate a fired heater.
Fired heaters and electric heaters use different units to measure output. A fired heater uses BTUs (British Thermal Unit) and electricity is measured in kilowatt hours (kWh). The output of one kWh is equal to 3412 BTU/h. If you have a 3 million BTU/h fired heater you would need an electric heater rated at 879.2 kWh to match the output. The fired heater on average would consume about $29 per hour of natural gas whereas the electric heater would consume about $61 per hour of electricity according to current prices for natural gas and electricity.
Renewable energy continues to get cheaper to generate while fossil fuels have reached their peak efficiency. The gap between the two is shrinking, but we may still be a decade or more from seeing the cost of electricity rival natural gas if it ever does.
Another consideration is fuel storage. Recent examples of disruptions in electrical power and fossil fuel supplies due to weather proves it’s wise to have a backup power source in case of emergency. Storing fossil fuels is a lot easier and cost-effective than storing electricity. It’s really not practical to store the amount of electricity you would need to operate a larger electric process heater currently. You could use a backup generator but the generator would be large and costly and would require storing fossil fuels to operate. A generator would also add to maintenance.
Finding a balance between being environmentally responsible and fiscally prudent can be tough, and it’s a decision that will only get harder with each passing year. For now, with new technologies that reduce emissions, it just makes more sense to use fired heaters where possible. Especially when higher energy outputs are required for your process.
Find Astec product availability nearby
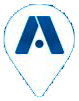