It’s a High Spec Job
As one of the leading aggregate producers in the state of Utah, Geneva Rock Products is no stranger to meeting tight specs on large-scale, complex projects.
Established in 1954 and headquartered in Orem, Utah, Geneva Rock Products has a long and rich history, making the privately-owned company one of the most respected contractors in the state. Originally put into operation to produce concrete aggregates for Geneva Steel in Orem, the company has expanded to offer its customers a wide range of related construction services and products. Today, Geneva Rock Products has 17 locations throughout the Wasatch Front region and is the largest supplier of ready-mix concrete in the state of Utah. It operates two hot-mix asphalt plants with production capacities of more than 400 tons per hour per plant, as well as two of the largest crushing plants in the state of Utah.
With a steady stream of work coming from the Utah Department of Transportation, Geneva Rock Products knows the importance of producing material that meets the strict specifications of the state. It's one of the reasons the company has invested in American-made equipment from a manufacturer it trusts with solid local dealer support, according to Ed Clayson, the company's aggregate production manager.
"We found that the equipment from KPI-JCI and Astec Mobile Screens helped us achieve those specifications by being able to manufacture equipment to produce that material," he said. "And we really enjoy our local relationship with Goodfellow Corporation – they represent their equipment very well, and they're making leaps and bounds in their service capabilities."
One of Geneva Rock Product's flagship locations is its Point of the Mountain Quarry, one of the largest quarries in Utah. To achieve its high production, Geneva Rock Products installed a variety of KPI-JCI and Astec Mobile Screens products, including six 3-deck screens, a Kodiak Plus K400+ Cone Crusher, a SuperStacker™ and a CS5260 horizontal shaft impactor.
"One of the main reasons that Geneva Rock Products has started purchasing a lot of KPI-JCI and Astec Mobile Screens equipment is because of the new innovations the company keeps coming up with," Clayson said. "It seems like KPI-JCI and Astec Mobile Screens is really striving to make great strides in improvements. I've had the opportunity to go through two of the factories, and was very impressed with the new innovations they are coming up with and how they take customer input and make changes to better their equipment."
To ensure their asphalt products meet the stringent specifications set forth by each state, producers must ensure particles are cubical, not flat and elongated. This cubicity specification is required to promote better binding of materials and increase the longevity of roads. When Geneva Rock Products decided to replace its 500-horsepower vertical shaft impact crusher with a new cone crusher to reduce wear costs and downtime and improve the quality of the material, the company had to first be convinced that the material would be able to meet Utah's specifications.
"We put the Kodiak Plus K400+ Cone Crusher on our dry plant, where we make all of our road base aggregates and our asphalt aggregates," on said. "We put this crusher in to replace a 500-horsepower vertical shaft impact crusher. Our biggest worry with the cone crusher was that our asphalt materials have to be 100 percent cubical product, but so far, we've been able to achieve that and increase our throughput.
"It's important for contractors like Geneva Rock Products to ensure that their specifications don't just meet the state's specifications, but really go above and beyond in their own specification requirement to ensure their material will meet any spec," Sy Harrison, sales manager for Goodfellow Corporation, KPI-JCI and Astec Mobile Screens' authorized dealer. "By producing high-quality material that is capable of meeting any requirement, Geneva Rock Products sets itself apart from other contractors and opens itself up to new opportunities in the market."
Recycling asphalt and concrete is an important aspect of Geneva Rock Product's operation. The company produces hundreds of thousands of tons of recycled concrete and asphalt each year. Using a portable, wheel-mounted CS5260 horizontal shaft impactor and a 8' x 20' three-deck screen to produce a 1/2 inchminus material, Clayson says Geneva Rock Products is operating "the best asphalt recycling plant that we've ever put together," Clayson said.
"We've experimented with quite a few in the past, so we're very happy with this operation," he said. "This is our second year of operation with this plant and it works very, very well."
In addition to a very successful 2012 – production ran 24 hours a day, seven days a week from Memorial Day to Thanksgiving – and a productive 2013, Clayson believes Geneva Rock Products will have an even more profitable 2014.
"We produced a lot of material in 2012 and 2013 throughout our company," on said. "We anticipate even more growth in 2014."
Request More Info
Find Astec product availability nearby
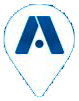