Production In Tow
Products
Industry’s only continuous crushing and tracking equipment combined with a tow behind conveyor cuts four months off project timeline.
In today’s fast-paced highway construction industry, there’s no margin for wasteful activity. So when Granite Construction discovered it could eliminate unnecessary and costly handling of material and save four months of labor by using the industry’s only continuous crushing and tracking impactor on a high-profile interstate project, it wasted no time making the switch to new equipment.
Granite Construction is one of the largest diversified heavy civil contractors and construction materials producers in the United States. The company has been in the business of building since 1922 – building everything from transportation, airports and transit systems to industrial, oil and gas and mining infrastructure.
Currently, Granite Construction is completing an 11-1/2-mile total reconstruction of I-40 and I-440 in southern Raleigh, N.C., according to Mark Schwandt, project manager for Granite Construction who is overseeing the construction project. The project involves removing the existing 40-year-old concrete pavement, crushing it to a 1-1/2”-minus recycled concrete Class 4 road base, and replacing with asphalt pavement.
After testing a number of brands in the industry, the company chose to purchase an FT4250CC track-mounted impactor plant and the newly-released tow-behind conveyor, which attaches to the rear and is powered off the track plant using a hydraulic drive. By pairing the FT4250CC with the tow-behind conveyor, the 1-1/2”-minus road base can be discharged over Jersey barriers, allowing the FT4250 to continuously crush and track forward and eliminating the need for trucks to haul crushed material for reduced operating costs. The discharged concrete road base is then smoothed over and prepped for asphalt paving.
“The continuous crushing that we can achieve with the FT4250 and the addition of the tow-behind conveyor allow material to stay in the work zone, which was critical for this project,” Schwandt said. “There was not an option to haul this material off site, crush it and bring it back in the restricted hauling hours that we have. We needed both machines to be able to meet our schedule.”
Results proven from the field have shown that producers can achieve more than $1 per ton savings by eliminating unnecessary haul trucks and replacing with the tow-behind conveyor, thereby minimizing the number of times the material is handled.
“Unnecessary material handling is a costly mistake,” said Jodi Heirigs, product manager for Astec. “By investing in a tow-behind conveyor, producers and contractors can achieve very significant savings over the lifetime of the machine.”
MEETING PRODUCTION
The process for the I-40 reconstruction project begins by breaking the existing interstate concrete pavement, which averages 48-feet-wide in each direction, and then processing the material to remove as much steel as possible. By processing the material first and breaking it down to a smaller size, Granite Construction is able to achieve maximum efficiency out of the FT4250CC, Schwandt said.
An excavator then loads the FT4250CC to crush to 1-1/2”-minus base material to lie underneath the new asphalt pavement. From there, the impactor plant moves forward every 12 minutes, building windrows of material directly where it would be used as road base using the tow-behind conveyor.
“Our production goal is to average 1,000 feet per day,” Schwandt said. “If we had to stop and shut the machine down before we tracked, it would be shut down every 10 minutes and then you would have to walk it forward and then there’s the time that you have to allow the machine to idle down – that just was not an option. Not with this.”
By using a continuous crushing and tracking impactor, the company is able to save a minimum of 20 percent of downtime, which Schwandt estimates will save the company at least four months of labor over the lifetime of the project.
The size of the impactor’s screen was another key factor in the purchase decision, Schwandt said. The 6’ by 12’ double-deck screen – the biggest screen on a track machine in the industry – enabled Granite Construction to meet its production goals and stay on schedule.
“Having the FT4250 allows us to control our schedule, which was very important for this project,” Schwandt said. “It’s on site when we need it and it allows us to monitor the quality of material better, which is critical when you need to create a North Carolina Department of Transportation spec product.”
CONCRETE CHALLENGES
Granite Construction has faced a number of hurdles during the reconstruction project, including working in the middle of the interstate median, a tight space that required minimal machinery to complete the job.
“We are working in a very constrained space, which we really needed one piece of equipment that could do it all,” Schwandt said. “The FT4250 allows us to crush and screen at the same time, which means a second machine is not required. That’s perfect for us, because we just don’t have the room for extra equipment.”
Another significant challenge facing the company was the presence of solid steel dowel bar baskets embedded in the existing concrete. The dowel bar baskets are 1-1/8” by 18”, and Granite Construction approached the project concerned about crushing the concrete with the dowel bars intact.
“We were very concerned about the rebar going through the crusher,” Schwandt said. “This has not been a problem for us with the FT4250. The machine has a magnetic belt that pulls the rebar off to the side, which we later pick up and recycle. It’s worked very well for us.”
DEPENDABLE SUPPORT
Granite Construction has a longstanding relationship with Astec Industries, parent corporation to Kolberg-Pioneer, Johnson Crushers International and Astec Mobile Screens. Knowing the three companies were part of the Astec Industries family of companies gave Schwandt the confidence to try their products, he said.
“We have had very positive experiences with other Astec companies and have received great service from Kolberg-Pioneer, Johnson Crushers International and Astec Mobile Screens,” Schwandt said. “We appreciate that it’s an American-made product, as it helps us greatly when receiving spare parts.”
“When the FT4250 first showed up, we had a Kolberg-Pioneer service technician on site to train our personnel – many who had no experience with crushers in the beginning – and has come back on several other occasions,” Schwandt continued. “If we need parts immediately, we can get them the next day. Having that kind of consistent support is crucial when you are managing a high-priority, high-profile project like this.”
About Granite
Through its offices and subsidiaries nationwide, Granite Construction Incorporated (NYSE:GVA) is one of the nation’s largest infrastructure contractors and construction materials producers. Granite specializes in complex infrastructure projects, including transportation, industrial and federal contracting, and is a proven leader in alternative procurement project delivery. Granite is an award-winning firm in safety, quality and environmental stewardship, and has been honored as one of the World’s Most Ethical Companies by Ethisphere Institute for seven consecutive years. Granite is listed on the New York Stock Exchange and is part of the S&P MidCap 400 Index, the MSCI KLD 400 Social Index and the Russell 2000 Index. For more information, visit graniteconstruction.com.
Find Astec product availability nearby
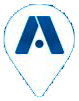