Production Meets Performance
The recent passage of Texas’ Proposition 7 – the single largest increase in transportation funding in Texas’s history – means one thing for aggregate producers in the Lone Star State: Focusing on production is more critical than ever.
For Charlie Harvey, crushing superintendent of Big Creek Sand and Gravel in Borger, Texas, achieving the high production needed to meet recent demand meant investing in new equipment that could double – and in some cases triple – the operation’s production.
Big Creek Sand and Gravel, formerly known as E.D. Baker Company, has been in operation for more than 20 years. The company offers a variety of services, including commercial aggregate sales, trucking, asphalt paving, earth work, wind generation work, highway construction and airport construction. Some of its major clients include the Texas Department of Transportation, Brazos Wind Ranch and Conoco-Phillips Company.
Knowing the company needed to increase production to meet demand, Harvey began searching for a crushing spread that was highly portable, durable and high performing. After researching competitive units, Harvey found a system that worked perfectly for his needs – the SM2650 Vanguard Jaw Crusher and the new K300/6203CC portable crushing and screening plant, purchased from authorized dealer Texas Bearing Company in Amarillo, Texas.
One of the key features that drew him to the Vanguard Jaw Crusher was the hydraulic dual wedge closed-side-setting (CSS) adjust, which eliminates manual shims and provides quick adjustment and enhanced safety. The ability to adjust on the fly increases production by several hundred tons every time an adjustment is needed, Harvey says.
“With our older Eagle crusher, it takes half a day just to adjust it manually,” he said. “With the Vanguard Jaw Crusher, you’re going within minutes. Not only is there a huge time savings, which equals more production, but realistically, you have to consider if the crew is going to take the time to shut down and spend half a day adjusting it every time it needs it. On a 110-degree day, the guys are going to run it with the jaw opened up before they adjust it, which hurts your production.”
At Big Creek Sand and Gravel’s operation, the Vanguard Jaw Crusher feeds directly into the K300/6203CC, a newly-released plant that combines a heavy-duty, roller bearing Kodiak® Plus K300+ Cone Crusher with a triple-shaft, low-profile horizontal screen. In its closed-circuit configuration, the K300/6203CC allows producers to utilize a single chassis to produce up to three finished products or supplement existing demand in a small footprint, reducing the number of auxiliary conveyors required to get the job done.
Harvey estimates his old Nordberg HP200 produces less than 40 tons per hour making 3/8”-minus rock. By using the Kodiak Plus K300+, that number tripled, he says. When making 1-1/4”-minus material, his production increased so much that his Kawasaki 80ZV loader couldn’t keep up, requiring him to switch to a larger loader.
“We couldn’t feed material fast enough making 1-1/4”-minus,” Harvey said. “Even our larger Kawasaki 92ZV loader couldn’t keep up. We had to have our other loaders come back in and throw a bucket in whenever they had time.”
SCREENING VERSATILITY
The addition of the new crushing spread meant additional screening power was needed on site, so Harvey sought out a mobile screening plant that could keep up with the increase in production.
Already familiar with the GT205S – in 2012, the company purchased the very first GT205S from Astec – Harvey decided to invest in a second unit. The GT205S is a double- or triple-deck track-mounted screening plant ideal for producers processing sand and gravel, top soil, slag, crushed stone and recycled materials.
Harvey uses the GT205S to process concrete rock and hot-mix material. By utilizing three screen decks, he is able to make A4 rock, a size of material the company previously had to discard. Now, Big Creek Sand and Gravel is able to avoid wasting material and can offer more products to its customers, he said.
“With our old two-deck screening plant, we were limited with the products we could make,” Harvey said. “The three-deck screen allowed us to make a product that is in demand that we were previously wasting.”
The GT205S has also proven to double screening capacity, compared to the company’s old two-deck screening plant, Harvey said.
“Our pit has quite a bit of sand in it, and with the triple-deck screening plant, we get much better screening capacity and can remove a lot more sand than we could with the regular two-deck screen,” he said.
DEPENDABLE SUPPORT
While achieving high production and performance has made a significant difference to the company’s operation and bottom line, at the end of the day, Harvey puts the most stock in the service and support he receives from the manufacturer and dealer.
“With Astec, everything is made here in the United States,” Harvey said. “Maybe that doesn’t matter to some people, but it means a lot to me. The people are right here to help you work through any problems, and you don’t have to wait on parts being shipped from overseas or deal with metric conversions. It just makes life easy.”
“It’s like anything else – you want to do business with people you trust and that you know are going to take care of you,” Harvey said. “I’ve been doing business with Texas Bearing Company for 35 years. And in those 35 years, they’ve never let me down. We have very little downtime because they are willing to get us parts quickly – sometimes in a matter of hours. Any time we need something, they are right there to help us – and at the end of the day, that means more money in our pockets.”Find Astec product availability nearby
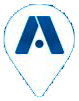