Short-term Challenges, Long-term Outlook
Highlights
Geneva Rock Products, | |
---|---|
![]() | Location: |
![]() | Material: |
![]() | Equipment: |
![]() | Final Products: |
The Challenge
After years of planning and regulatory navigation for a new quarry site, what do you do when you’re ready to start producing, but the supply chain is disrupted? This is the challenge Ed Clayson with Geneva Rock Products had to overcome with Black Rock Quarry, an operation overlooking the Great Salt Lake in Utah. Goodfellow was able to support Geneva in obtaining the right equipment for the job.
Getting Started
Anyone with experience will tell you setting up a new site can be a long process requiring the alignment of a host of considerations. From site selection and exploration to permitting and approvals, there is a lot to manage. For Geneva Rock Products, the launch of its Black Rock quarry met several obstacles along the way.
Founded in 1954, Geneva Rock Products started as a ready- mix concrete supplier, providing concrete for the Wasatch Front. Over the following decades, the company expanded into aggregates, asphalt and construction services, becoming one of Utah’s largest construction firms. With 70 years of history, Geneva is recognized for its commitment to quality and innovation.
This outlook toward innovation includes strategic site identification and long-term planning. The Black Rock quarry acquisition required several years of negotiation, leaving them eager to get started when it was finally completed.
“There were quite a few T’s to cross and I’s to dot for an agreement to mine on this property,” says retired Area Manager for Geneva, Ed Clayson. “The main interest in this property for Geneva Rock was a location to service the northwest quadrant of Salt Lake County and Tooele County. When the production team put boots on the ground, we realized we were going to have some challenges. It is a limestone quarry with very large boulders that can be incredibly unforgiving.”
These hurdles did not slow them down thanks to the support of Geneva’s equipment dealer, Goodfellow Corporation, and equipment manufacturer, Astec Industries. Together, the team created a plan of action and selected the equipment now running on the site. This includes a BTI BXR120C rock breaker for breaking up the large material, a portable CS3365 Pioneer® jaw crusher plant, equipped with a BTI rock breaker boom system which feeds to an Astec 8’ x 24’, three-deck horizontal screen. From the screen, throughs are stockpiled while overs are sent to a Kodiak® K400+ cone crusher for further reduction.
“When we were going through the equipment selection process, Geneva was very specific on what they wanted and the production/portability goals they were aiming for. We were able to partner with Goodfellow and supply our CS3365 portable plant, along with our K-400+ Kodiak cones and 8243-38LP screeners on custom Goodfellow chassis for their spread. We also added the precautionary BTI boom system on the CS3365 after Mark 'GRONK' Hansen & I visited with Ed & Ken onsite and saw the onsite footprint challenges and the massive boulders within their cut.” says Bill A. Royce, Regional Sales Manager with Astec.
The quarry began operations in late 2022 with a six-man crew producing state spec road base, including a 2-inch drain rock and a 3-inch fill product.
“When we first started putting this all together, it was just shortly after COVID and there was quite an equipment shortage. We proactively ordered our equipment in advance. We had a master plan for the future, not knowing how long it was going to take us to develop this footprint. So, we have started with a very small footprint. Our current process is to produce material we think would be a fast seller. From there, we plan to install more equipment to provide a greater variety of products,” explains Clayson.
“We were elated to meet our 2023 goal. Next year the goals go up. We’re focused on developing our customer base and working to get more visibility here,” says Clayson.
Equipment Overview
Portable CS3365 Pioneer® Jaw Plant: Ideal for primary crushing, handling large, challenging rocks.
“While we were shopping for a primary, Goodfellow took us to see a few other 3365 jaws around the area. We talked to the operators there and they were very happy with the way they work. We thought with the challenges we’re going to have here with the big rock that the 3365 was going to be the right jaw for the job. “
Astec 8’ x 24’ Three-Deck Horizontal Screen: Crucial for efficient material separation and sizing.
“This is the first 8’ x 24’ screen that Geneva Rock Products has operated. It does an excellent job and has a lot of screening capacity. It does exactly what we need it to do for us.”
Kodiak® K400+ Cone Crusher: Ideal for secondary crushing applications where further sizing and shaping are required.
“A few years ago, I was given the assignment to go out in the field and investigate cone crushers and determine the best cone crusher on the market. I was able to make several trips around the country, and we looked at a lot of different cone crushers out on the market including the pros and cons of both roller bearing and bushing cones. We took a visit to the Astec factory in Eugene, Oregon to see the Kodiak cones. I must admit I didn’t have high hopes in seeing what I would like, but they were able to answer all my questions and address all the concerns we had about the Kodiaks at the time. They changed my perspective on the cones and, at the end of it all, we felt strongly that the Astec cones were the right fit for us.”
Jaw-Mounted BTI Boom System: Essential for breaking down oversized rocks prior to entering the jaw.
“We also put a mounted breaker onto the jaw in case we have any oversized material that needs to be broken down. Though we don’t have to use the breaker too often, we are glad that we have it as a safety net. If a piece of material enters the crusher that is too large, it could cause hours of downtime getting it removed.”
Customer-Focused Support
The long-standing relationship between Geneva and Goodfellow allowed for unwavering support throughout the launch of Black Rock quarry. From equipment selection and consultation to installation and maintenance, the Astec and Goodfellow expertise helped Geneva Rock navigate the supply chain challenges and attain operational efficiency.
“I have the opportunity to work with a lot of people at Goodfellow corporation,” says Clayson, “and their service is impeccable. When we purchase new equipment, we have several things to consider, and the most important is service. We do a lot of our own maintenance, but we do have instances where we call Goodfellow. They are reliable and almost always have the parts we need . Any time we are down, the most important thing is to get back up and running. You can’t do that if parts aren’t available.”
“Goodfellow and Geneva have partnered on parts and service for decades. We are intimately familiar with their large operations across the region. With our close insight and relationship, we are able to anticipate their needs and ensure we have everything they need to stay productive,” says Mark Hansen of Goodfellow.
Astec was right alongside Goodfellow on this journey. “One thing I really like about Astec is that they address my concerns. I can take a laundry list of items to them, and we will set up a call to review what needs to be addressed,” says Clayson.
The Road Ahead
Though Geneva is just getting started at the Black Rock quarry, additional plans for the site include the construction of a batch plant for ready-mix concrete.
“We’re hoping someday to be one of the most impressive setups in operation. Geneva Rock Products is an innovative company. We do a lot of things that are not standard in the industry. One example is our downhill conveyor system at the Point of the Mountain that sets us apart from others. Coming downhill on an 18.66-degree incline, we can generate power with that system. We like to be as sustainable as possible,” says Clayson.
Launching the Black Rock quarry was a formidable challenge with several obstacles to overcome. The collaboration between Geneva Rock, Astec and Goodfellow demonstrates the power of resilient planning, innovative solutions and reliable partnerships. Geneva Rock’s successful adaptation to changing conditions highlights the importance of robust equipment and dedicated support in achieving operational excellence.
Find Astec product availability nearby
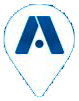