Taking Advantage of an Upgrade Opportunity
Shell replacement at Vulcan Materials Co. in Tucson provides for more RAP use
As long as the shells were being replaced, Vulcan decided to upgrade the drum, including installing a purge door, adding a temperature switch to shut off the burner in case of fire in the drum, and installing a thermocouple that tells the plant operator the temperature of the outer shell so he can read it in the control house.
Astec Double Barrel Drum Mixer
Highlights
Country / Region | USA |
---|---|
Installation Site | Tucson, Arizona |
End User | Vulcan |
PROJECT | Drum Shell Replacement |
Application | Asphalt Mixing |
DRUM TYPE | Double Barrel Dryer/Mixer |
Products
Plants as busy as Vulcan Materials Co. in Tucson, AZ, are eventually going to have to replace the inner and outer shells on their Double Barrel drum mixers. The wear and tear of aggregate drying in the inner drum and of aggregate being mixed with asphalt binder in the outer drum eventually require that the shells be replaced.
“The shells are wear items,” says Mike McClure, Astec salesman. “It’s completely normal to replace them for drums drying on the inside and mixing on the outside.”
McClure, who handled the sales and specifications for the Vulcan retrofit, says that when Vulcan recognized it was time to replace the shells, they asked themselves two questions: When can we shut that double drum down without impacting our business? And, since we’re replacing the shells, what upgrades can we make to improve on the products we offer?
“The drum was completely worn out,” says B. Jay Pitts, who at the time was plant manager over three Tucson asphalt plants for Vulcan Materials and oversaw the replacement of the inner and outer shells. “We’d patch it in between hot stops and overnight we would patch it. We’d just have to open the shell and go in the drawer and patch the hole.”
Because paving is a year-round activity in the Southwest, taking the plant out of production would impact the tonnage Vulcan could produce. McClure and Pitts say Vulcan determined the best time to pull the plant offline was late November.
“We spent some time trying to pick the right time to do it,” says Pitts, who today is a plant manager for Granite Construction. “We decided that was the best time we had.”
Opportunity for Upgrades
The Double Barrel drum was bought in 1991 and the inner shell was replaced in 2004. It provided another 14 years of constant use before both inner and outer shells were replaced in 2018.
Working with McClure, Pitts ordered the drum and the Astec team visited the plant to take site measurements and firm up the specs. Astec built the drum to Vulcan’s specs and once it was done transported it from Chattanooga to Tucson, pilot cars shepherding it and stopping at all the weigh scales along the way.
McClure says that Vulcan decided that as long as the shells were being replaced, they would upgrade the drum to more modern stands. Improvements included:
Installing a purge door, which lets fresh air in during the purge cycle of the burner so that any gases that might have accumulated are forced out before the burner is lit.
Adding a temperature switch to shut off the burner in case of a fire in the drum. The switch puts limits on the burner and if the temperature reaches 450°F on the outer shell, the temperature switch automatically shuts the burner off.
Installing a thermocouple that tells the plant operator the temperature of the outer shell so he can read it in the control house. “Usually that’s what ruins your outer shell,” McClure says. “You can have a fire in there all day long and never know it until you see the color change on the drum.”
A Strategic Installation Plan
Astec’s McClure, Don Schell, service department, and Travis Sneed, parts department were involved throughout the installation process. Pitts says that to ease and speed the installation, Vulcan Materials brought in people from other Vulcan plants. Pitts divided the available workers strategically into groups and each group was responsible for only one aspect of the installation. For example, one group was responsible for removing insulation from the old drum, one group was responsible for removing and replacing the four trunnions and thrust rollers, one group handled the chains and sprockets, and one group handled the drive trains.
“Each group worked on its own piece and they didn’t have to worry about anything else,” Pitts says.
Pitts says they started each day with a safety meeting, outlining work that was going to be done that day and highlighting specific safety hazards.
Because of the strategic division of labor, they were able to completely strip the drum the first day.
“We stripped it all down to the point where the bottom tray was still there, but the outer shell was off,” Pitts says.
Vulcan hired a 90-ton and a 125-ton crane to lift the old shell and reposition the new shell, and on the second day the inner shell was removed and placed on a low-boy trailer and hauled away. “After the old drum was off, we pulled the belly pan off the chassis,” Pitts says.
The Vulcan team then spent two days getting the trailer cleaned up and improving the structural integrity of the chassis.
On day five the team set the pan, set the drum, set the outer shell complete with new chains and sprockets. Then they fired it up for a test.
“We tested it and trained it to ride right in the middle empty and then we trained it again to ride right in the middle when full of mix,” Pitts says.
Modification Means More RAP
Designed originally as a combination plant that could be used to dry aggregate on the inside or operate as a Double Barrel, Vulcan decided to use the retrofit as an opportunity to upgrade the plant. McClure says the first decision they made was to convert the plant from a combination plant to a plant that dried. That meant removing the gate, which McClure included in the new shell specs.
Eliminating the gate freed up three feet of space, and McClure suggested the plant could accommodate more RAP if they moved the conveyor.
“They could take advantage of that space because they were replacing both the inner and outer shells at the same time,” McClure says. “All Double Barrels are rated to run up to 50% recycled material under certain conditions, and one of those conditions is the amount of moisture in the RAP. An extra three feet means you can get rid of more moisture than they could before, and they can get rid of the moisture quicker. Now it’s easier for them to run a higher percentage of recycled hot mix.”
Find Astec product availability nearby
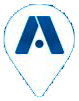