The Importance of Asphalt Plant Maintenance
Scheduled maintenance at the asphalt plant helps to prevent failure while also ensuring the facility is running at peak performance. All planned maintenance work should be detailed by the OEM/equipment suppliers and Astec provides our partners with optimal maintenance schedules/plans and procedures for our equipment.
Hot mix asphalt facilities are complex electrical and mechanical systems with thousands of moving parts. Any electrical or mechanical failure can lead to a plant breakdown. That’s why proactive and preventive facility maintenance is essential for reliable performance at your asphalt plant. Well-maintained plants encounter fewer extensive repairs and breakdowns while improving operating costs and boosting customer retention and satisfaction.
For this reason, asphalt plant maintenance should be a daily, top of mind task with additional downtime scheduled to inspect and complete needed repairs.
"Asphalt plant owners who develop year-round maintenance processes for their facilities ensure that they will meet or exceed customer expectations and promote the growth of their business," Daniel Francisco, group director service, Integrated Process Solutions at Astec Industries, Inc. says. "Neglecting the maintenance of any key plant components will increase the risk of failure."
Scheduling time for maintenance also ensures things are running at peak performance as plant maintenance allows you to take some time and see what might be ready to replace or in need of lubrication, adjustments, recalibration, etc. Scheduled plant maintenance has to do with not just maintaining the machine running, but also maintaining it running efficiently and accurately.
"Owners who develop year-round maintenance processes for their facilities ensure that they will meet or exceed customer expectations and promote the growth of their business," Francisco says.
Complete Maintenance Checks
Every asphalt plant has a scheduled maintenance checklist and it's important to rely on that guide and follow service intervals to ensure your plant is ready to meet the demand that are placed on it each day.
"Neglecting the maintenance of any key plant components will increase the risk of failure," Francisco says. "However, here at Astec, our experience is that most failures are linked to air systems, combustion systems, electrical systems and wear parts."
The frequency of your maintenance varies for every component in a plant. Astec provides maintenance schedules that range from daily to annually, offering every interval in-between. Maintenance records should help you tailor a maintenance schedule that matches your facility.
"Promoting a good maintenance culture leads to fewer plant breakdowns," Fransisco says. "Documenting and maintaining maintenance records from your plant site is another important process in reducing plant breakdowns. Using a hands-on approach and conducting thorough plant assessments and inspections, allows plant owners/operators to better manage and plan maintenance."
Safety Matters
When your equipment is operating correctly, it will also improve safety at the plant.
"Poorly maintained plants lead to serious injuries and workplace fatalities," Francisco says. "Well-maintained plants that invest in personnel training for OSHA, MSHA, Lock Out-Tag Out, etc. promote a safer work environment that can reduce and/or eliminate those injuries and deaths."
And this can also help your overall operations as well and it boils down to ensuring those who work at the plant are given the time to make maintenance a priority.
'Neglecting any aspect of plant maintenance threatens smooth operations," Francisco says. "All planned maintenance work should be detailed by the OEM/equipment suppliers and Astec provides our partners with optimal maintenance schedules/plans and procedures for our equipment."
Upgrades Can Improve Quality
Conducting maintenance in the past used to be an incredibly manual process, but technology today has improved and therefore so has tracking and scheduling maintenance.
"Advanced technologies such as plant control systems and automation are on the cutting edge of downtime mitigation," Fransisco says. "As an example, the powerful computer/PLC-based control systems from Astec allow customers to easily and efficiently monitor data and manage plant operations. As for predictive maintenance items, plant managers, if they have cultivated a strong maintenance culture, could address several of these items during downtime."
These new systems help control downtime so your plant can be up and running as soon as maintenance is conducted.
Partnering for Success
If your asphalt plant does breakdown, having a good partner is key to getting back up and running quickly.
"Getting a plant up and running quickly doesn’t happen if plant owners are thinking reactively," Fransisco says. "If plant owners want to get a plant up and running in the shortest amount of time possible, they need to think proactively. Having an inventory of parts and skilled personnel trained and ready before a plant breakdown is critical to minimizing downtime. Partnering with a good manufacturer, like Astec, not only assures quality products and superior engineering, but it offers the parts and service expertise needed to limit downtime."
At the end of the day, routine maintenance, if performed correctly will help your plant continue to run smoothly and profitably.
"Maintenance is a necessity that you can’t afford to overlook, and proper maintenance begins long before a plant breakdown. Leveraging a strong maintenance culture at your facilities will reduce downtime and maximize your profit margins," Francisco concludes.
Find Astec product availability nearby
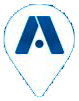