The Right Element
The ability to quickly adapt to unforeseen situations is key to thriving as a producer in a tight job market. But for Gene Henrie, owner of Quality Crushing, conquering unexpected challenges is just part of the job.
When Henrie first contracted to crush ore for CS Mining, LLC, a copper mine near Milford, Utah, the job required him to produce 3/8”-minus material from two ore bodies. Four months into the project, the crushing producer was asked to meet a ¼”-minus spec from a wider range of ore bodies to increase production through the ball mill and assist in the flotation and grinding processes. With the help of his local dealer Goodfellow Corporation, Henrie was able to meet the demands of the job with ease and help increase production of the plant.
“We really didn’t know if we could make that specification work in the beginning,” Henrie said. “It’s something we have never been able to do before. But we’ve been able to meet their spec and it’s really helped their production.”
To produce the end material, a copper concentrate, Henrie first processes the shot rock through a jaw crusher, then conveys the material to a secondary cone crusher fitted with a medium-fine liner, and finishes with a tertiary cone crusher fitted with an extra fine liner. The crushed ore goes from the stockpile directly into the ball mill, a large, rotating drum in which the ore is ground to an even smaller size by using steel balls and water. The resulting slurry is then pumped into a flotation separator, where the non-copper bearing minerals and waste material are removed.
To accomplish this, Henrie utilizes an extensive spread of Astec equipment, including four 7’ x 20’ horizontal screens, two 6’ x 20’ horizontal screens, an 8’ x 20’ horizontal screen, four Kodiak® Plus K400+ Cone Crushers, a Kodiak® Plus K300+ Cone Crusher, two 3144 Vanguard Jaw Crushers and two SuperStacker® extendable stackers.
Henrie obtained his equipment from Goodfellow Corporation, an Astec dealer with locations in Utah, Nevada and California, and worked closely with the dealer to design a plant layout and test the equipment to ensure he was able to meet 100 percent passing ¼”-minus. Once confident he could meet the desired spec, Quality Crushing began working with six ore bodies to crush the ore for the copper mine. The company is currently producing about 1,800 tons per hour per day, on a 10-12 hour shift, Henrie said.
In addition to meeting a challenging spec, Henrie says one of the biggest challenges with processing ore is managing the diversity in material in each ore body. To overcome this, Henrie has worked closely with Goodfellow Corporation to be able to continually adjust the screens and the cone crushers to achieve the best production.
“One of the things we’ve been doing with customers like Gene in finishing screen applications is adjusting the screen and the stroke to match the material, screen sizes and feed size,” said Sy Harrison, sales manager for Goodfellow Corporation. “By doing this, we’ve been able to adjust the finish screen and give them 10-15 percent more production of that ¼”-minus material that was being produced by the crushers but not being pulled out by the screens.”
“We like to look at the screens as the cash register, where you tally up at the end of the day how much material you actually made, and in order to do that, we have to adjust the screens accordingly,” he added.
Henrie selected the Kodiak® Plus cone crushing product line because of its ability to succeed in all applications, he said. Here, he runs the K400+ cone crusher in a tertiary application at 950 RPM with an extra fine liner, and the K400+ cone crusher in a secondary application at 900 RPM with a medium fine liner, which enables Henrie to produce the maximum amount of ¼”-minus material.
The hydraulic tramp iron relief system on the Kodiak® Plus Cone Crushers also proves beneficial in ore crushing applications, as the crusher is forced to process a variety of uncrushable material such as drill pieces. The Kodiak® Plus cone crushing products utilize a unique, patented tramp iron pressure relief system that protects the machine from tramp iron events and eliminates the maintenance costs and violent back pressure associated with accumulators. The product line also features a precision roller bearing design as well as a new hybrid cast/fabricated base frame design, the ‘MILO’ automated control system, a new patented liner retention system, patented thread locking ring and anti-spin cone brake.
“These cones, they can handle whatever we throw at it,” Harrison said. “The hydraulic mechanism works well, and it allows for a long bearing life and a long crusher life because of it.”
Like any machine, the equipment can only function as well as the operator, and Harrison said Henrie is diligent in both balancing the plant and maintaining his equipment, which is critical to his success.
“Gene does an excellent job in making sure both cone crushers are choke fed, which is all you can ask for in these kinds of applications,” Harrison said. “Because of that, he’s able to sustain a high average for tonnages per hour. He’s also fantastic at maintaining the equipment and making sure it’s up and running every day. As a result of his dedication to maintaining the equipment and constantly ensuring the equipment is set up in a way to achieve the best production, he’s been able to be tremendously successful in this application.”
Find Astec product availability nearby
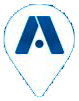