The value of thermal fluid heaters
Finding the right thermal fluid heater depends on more than just price. When acquiring a thermal fluid heater, several factors should be considered in addition to heat output. To get the most for your money you need to pay special attention to things that affect the life of the heater and the life of the thermal fluid it heats. Unfortunately, a lower initial cost tends to make buyers overlook these factors.
Highlights
Thermal fluid heater buyers should pay special attention to several things when evaluating a heater:
- Flux rate
- Combustion loading
- Radiant surface area
- Convection surface area
- Corrosion allowance
- Control system
A closer look at each will prepare buyers for selecting a heater that offers effective thermal performance.
Finding the right thermal fluid heater depends on more than just price. When acquiring a thermal fluid heater, several factors should be considered in addition to heat output. To get the most for your money you need to pay special attention to things that affect the life of the heater and the life of the thermal fluid it heats. Unfortunately, a lower initial cost tends to make buyers overlook these factors.
The higher initial cost of a heater may be more than offset by its longer life. Moreover, the value gained by reducing deterioration of the thermal fluid also should be factored into the costs.
Poorly designed heaters usually have lifespans of only 5 to 10 years and may cause frequent breakdowns of thermal fluid and equipment. Well-designed heaters should last 20 to 30 years and rarely need thermal fluid replacement.
Flux Rate
In order to understand flux rate it is important to first consider how a fired heater heats the thermal fluid. The heat is generated by the combustion of fuel, which produces a flame and hot gases. The burner flame produces radiant heat energy while the gases produce convection heat energy. Both the flame and gases transfer heat energy to a metal pipe coil through which the thermal fluid flows. The section of the pipe coil exposed to the flame is heated by both radiant energy and convection energy. The shielded section of the pipe coil is heated by the convection heat energy only.
Flux rate is defined as the rate of heat energy—both radiant and convection—transferred through a unit area of the pipe coil. It is stated as BTU per hour per square foot. If the coil has fins, you should disregard the extra surface area added by the fins and instead, use the surface area of the bare pipe. In short, the higher the rate of energy through a given surface area, the higher the flux rate is. Higher flux rates produce coil surface temperatures that are higher than those produced by low flux rates.
Coils last longer when exposed to lower temperatures due to lower flux rates. Lower flux rates also cause less deterioration of the thermal fluid, so it lasts longer. The one drawback to lower flux rates is that more surface area is needed to achieve the required amount of heat transfer. Accordingly, more surface area is achieved by using a larger coil, which adds to the initial cost of the thermal fluid heater.
When comparing heaters, it is important to compare flux rates. Heaters with lower flux rates should last longer than heaters with higher flux rates but typically they cost more. The equipment longevity provided by lower flux rates typically more than offsets the initial cost difference of a larger coil.
Thermal fluid heater users should be concerned with three types of heat flux rates:
- Overall average flux rate
- Average radiant flux rate
- Maximum radiant flux rate
Overall average flux rate considers both the radiant and convection surface areas. It is determined by dividing the output duty of the heater by the total heating surface area of the coil.
Average radiant flux rate is based on the total area of the coil surface exposed to radiant energy from the flame. It is an average of the energy transfer rate, which will vary from one end of the coil to the other.
Maximum radiant flux rate occurs in the area of the coil surface exposed to the greatest amount of radiant energy from the flame. In a helical coil heater, it is typically an area of the coil about one-third the way along the inside of the coil length.
All three types of flux rates affect the maximum film and metal temperature.
Combustion Loading
Also known as volumetric heat release, combustion loading is defined as the BTU-per-hour input divided by the net volume of the radiant section, excluding the coils and, where applicable, refractory dividing walls and other elements. It is stated as BTU/hour per cubic foot.
High combustion loadings tend to increase the radiant flux rate and increase risk of unwanted flame impingement on the heating coil. Therefore, the combustion chamber should be sized to contain the flame without impingement and to keep flux rates within acceptable limits.
Radiant and Convection Surface Area
Radiant surface area is defined as the total number of square feet or coil surface area exposed to radiant energy. Smaller surface areas produce higher flux rates.
Similarly, the convection surface area is defined as the total number of square feet of coil surface area exposed to convection energy. Smaller surface areas produce higher flux rates.
Corrosion Allowance
Corrosion allowance is defined as extra pipe wall thickness needed to maintain the integrity of the pipe coil after corrosion has taken a toll. It is a major factor in how long the coil will last if other factors are equal. All pipes are subject to some corrosion, which may vary widely depending on operating conditions.
Control System
Controls play a significant role in the life and operating cost of a heater. Three types of burners and controls are commonly used on thermal fluid heaters:
- Fully modulating
- Low-high-low
- On-off
Fully modulating burners with modulating controllers provide optimum fuel usage and the longest heater life. They closely match the burner output with the changes in heat demand. This avoids temperature under and overshooting, which is inherent in non-modulating burner systems. Moreover, optimum temperature controls, along with safety limit devices, ensure that the heater will operate within the design limits.
In conclusion, the ideal heater for a particular application depends on all of the factors described. When comparing heaters, do not make your choice based solely on the initial cost. Instead, consider all the factors discussed and how they are apt to affect the life of the heater and the thermal fluid it heats.
Find Astec product availability nearby
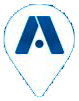