How Environmentally Responsible Roadbuilding Benefits Your Bottom Line
Highlights
The Astec ReMix CCPR system is a modular solution, comprised of the following components: |
---|
A core load with a trailer chassis, 300 TPH (nominal) pugmill, feed conveyor, controls system, water line connection, shore power connection, water pump & metering system, and either a foamed asphalt injection system or an asphalt emulsion injection system. The core load can be paired with a broad variety of other Astec components, including stand-alone feed bins, dust silos, asphalt tanks, and material loadout conveyors. |
As the industry starts shifting focus to a more sustainable future, many are left searching for the best way to balance being good stewards of the environment, while also keeping an eye on their bottom line.
For Astec, a global manufacturer of road construction solutions, one solution is the Astec ReMix™ Cold Central Plant Recycling (CCPR) System.
The new system gives producers the tools they need to meet the challenges of modern roadbuilding projects while also prioritizing environmental responsibility.
Get an inside look at Astec’s latest innovation and find out what the team believes lies ahead for the future of CCPR mix design.
Introducing the Astec ReMix CCPR
The Astec ReMix CCPR employs cold recycling technology, bringing a sustainable approach to construction that minimizes the environmental impact while also presenting an opportunity to utilize reclaimed asphalt pavement (RAP) stockpiles.
The Basics: CCPR vs. Hot Mix Asphalt
There are two key differences between CCPR and traditional hot mix asphalt.
First is the mix design. With CCPR, 96-plus percent of the material is recycled material. Only a small portion of virgin binder is added, as well as a small percentage of water. This gives producers a solution for what to do with RAP that doesn’t include a costly storage or disposal, especially if they are limited with how much RAP they can use in traditional mixes.
Second, the material is mixed at an ambient temperature. There’s no heater, significantly reducing the carbon footprint.
Substantially reducing the need for both virgin aggregates, virgin binder, and energy for heating the mix not only benefits your overall costs, it also conserves natural resources and lowers carbon emissions – reducing your carbon footprint.
CCPR can be used for high-volume interstate jobs, base levels for parking lots and everything in between.
Behind the Science
Now, CCPR isn’t necessarily a new topic, however, with recent shifts of focus to sustainability efforts at Astec and in the industry, the timing was perfect to bring this system to market.
“We have engineering memos from back in 2008, 2009, where some of our engineering teams were looking at ways to make a CCPR material out of our Double Barrel,” says Trevor Wagoner, Astec's Director, Sustainability. “Then, about two and half years ago, we really started talking in earnest about what we needed to do as an organization to develop a solution in this space.”
The first step was talking with people already working with this material. The ASTEC team set off to meet with producers in Alabama and Virginia to learn more about their experiences, what they liked and what could use improvement. Armed with this knowledge and their team’s continued work on the idea, they had their spark.
“The fact that we were able to go from a concept when we met with a producer in Virginia in March 2023 to having a product that we were able to launch at World of Asphalt this year, is a huge testament to the creativity of our engineering teams taking advantage of our existing knowledge and expertise,” says Wagoner.
Benefits of CCPR
- Designed for an American producer operating in an American market
One of the first things you’ll notice about ReMix is that it’s bigger than some of the other offerings. The Astec ReMix CCPR reliably churns out 300 tons per hour, meaning you can produce this material in meaningful quantities for those big jobs as well as smaller ones. - User-friendly interface
The system was engineered to prioritize user-friendly maintenance and operation. The layout and components make routine maintenance straightforward, minimizing downtime and maximizing the overall efficiency of recycling operations. - Modular Configurations
The Astec ReMix system offers a range of modular configurations, providing flexibility to asphalt mixing operations. Producers can configure the plant however they need, from a highly portable setup ideal for changing locations to maximum production configurations capable of handling large-scale road construction.
“Astec has a great reputation in the industry and the fact that we have developed something to support this type of mix design encourages producers because they know that we are going to be able to provide our technical expertise when they have to go to bat with their customers to try to promote this new technology,” says Wagoner.
Embracing a sustainable future
Even with an increased demand for sustainable practices in road construction, Astec knew that creating the Astec ReMix CCPR would only be the first step. There is still a lot of work to do.
“Everybody is kind of looking for somebody else to take the first step,” says Wagoner. “Producers don't want to invest in the material until the state is willing to specify it, but the state is reluctant to specify it until they have producers making it and demonstrating that it's a viable material that has all these benefits.”
To end this stalemate, the answer is simple: communication and education.
“I think the biggest thing is to just talk about it and bring it up your customers, your local and state government representatives and departments of transportation,” says Wagoner. “Anybody who has anything to do with the way that we build our infrastructure, the more people that are talking about it and are aware of it, it's so easy to understand why it's an attractive mix design.”
Helping move the conversation in the right direction is the fact that cold recycling mix has been tested extensively at the National Center for Asphalt Technology (NCAT) since 2012.
At NCAT, this material has gone through more than a decade’s worth of testing on the NCAT Pavement Test Track, a high-speed, full-scale accelerated pavement testing facility. During each 3-year research cycle, the track is subjected to 10 million equivalent single axle loads (ESALs) of heavy truck traffic applied over a period of two years.
Breaking that down further, at about 20,000 ESALs a workday for give or take 50 weeks a year, that would be 10 to 15 years’ worth of traffic on a typical interstate.
One of the results of all this testing is CCPR, a high-quality product that holds its own – in a variety of climates – while also minimizing the carbon output.
For Raymond “Buzz” Powell, who recently retired as an associate director and research professor at NCAT, building a good road is like a four-legged stool – you need good materials, good designs, good construction effort and good inspection. Cold recycling mix is most of the way there, however there is still one crucial part of the equation to work out.
“Over the last 12 years, we have validated the materials, the design, the construction practices and so now it's about implementing and enforcing a specification package in a competitive bidding environment that gives us the quality that we know we can produce with this material,” says Powell.
“The data speaks for itself,” adds Powell. “We know that it works. We've proven it in diverse climate applications and diverse moisture applications, so now it's time to get to work with implementing good specifications.”
Bolstered by this research and the successful Virginia Department of Transportation project on I-64, the Astec team is seeing the path forward for more widespread use.
While Virginia is the poster child now, Wagoner and the Astec team are starting to see interest from other states like Georgia, Indiana, Illinois, Michigan, New York, Vermont, New Hampshire and California.
“We are seeing a convergence of a lot of these challenges and in my opinion, the time is ripe for us to see a blossoming of CCPR mix design across the U.S. industry,” says Wagoner.
Find Astec product availability nearby
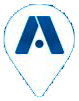