IntelliPac: Precision Moisture, Proven Efficiency
Highlights
The Astec IntelliPac™ Moisture System logs data and tracks historical trends which allows operators to make informed adjustments in real-time, resulting in a more efficient, cost-effective production process.
Dunn Construction found that this system not only improved moisture management but also enhanced their ability to maintain consistent asphalt mix.
As a result, Dunn plans to roll out the system across their other plants.
Products
How often are you having your moisture levels checked? If the answer is not as often as you should, you’re certainly not alone.
While many manufacturers recommend lab personnel take moisture measurements at least once per day, if not more, that’s simply not practical for many asphalt plants.
In the grand scheme of things, this seems like a relatively smaller piece of the puzzle, especially in comparison to everything else that needs to happen to keep a plant running. However, while this task is minor, it’s impact is mighty. If moisture measurements aren’t being accurately captured and adjustments made, the costs can really add up.
And that’s the real kicker – it may not seem like a significant cost issue in the moment, but when you have the data and can look back to see the costs associated with under or overdosing liquid asphalt into your mix, you will have a whole new perspective.
This was the case for Alabama-based Dunn Construction.
After partnering up Astec, the Dunn Construction team is looking at operations in a whole new light, with more confidence that their plants are operating at peak performance.
Let’s talk about why.
Teaming up to solve an industry pain point
Moisture sensors specifically for asphalt production isn’t anything new. However, many iterations have fallen short in the past.
Why? Well for starters, asphalt plants can be a brutal environment for technology. Not only would a sensor need to capture accurate and consistent moisture readings, but they must also withstand harsh conditions.
After years of research and development, the Astec team created what would one day become the Astec IntelliPac™ Moisture System. This automated solution was designed to endure the demanding conditions of an asphalt plant so that operations could perform at peak levels without hassle.
The science driving it was there, the results in the lab proved encouraging. Only one thing remained: testing it in a real-world application.
The IntelliPac System walks the walk
It’s one thing to say the IntelliPac system provides unparalleled visibility into virgin aggregate moisture levels, ensuring accuracy and reliability in the asphalt production process from the lab.
Out in the field is another matter altogether.
As a powerhouse in the asphalt production space, Dunn Construction was a perfect fit to give the IntelliPac system a proper run.
“At Dunn Construction, we look at continuous improvement as an everyday goal,” says Mike Fields, plant/aggregates operations manager for Dunn Construction. “We made a decision to collaborate with Astec on this system, simply because we trust their company, and we worked with them for years on many different projects.”
It didn’t take long to start seeing the benefits of this collaboration.
“Immediately we saw accuracy. Immediately we saw [the system’s] capability to track and control quality. It improved our quality in the lab immediately,” says Fields. “In all the time I've been watching asphalt plants run and being involved with this I've never seen as consistent results in the lab as I have with this [IntelliPac].”
The Astec team was heavily involved, working closely with the Dunn Construction team to ensure the sensors were installed in the best position for the plant and getting all the necessary readings. This took some fine tuning.
“In the past, we were using our liquid asphalt gauge to monitor what percent asphalt we were actually putting into the mix design,” says Donnie Strickland, asphalt mix designer at Dunn Construction who oversees quality control. “During my testing with Astec, I gathered aggregates from the conveyor belts and bins to bring them back to the lab to check moisture levels and that's how we kind of dialed the sensors in.”
Once the sensors were dialed in and testing began, the team received some valuable insights within the first few weeks.
“After we initially set up, I got a call from Donnie that the AC was running really high, and that had been abnormal,” says Paul Bowden, plant superintendent at Dunn Construction. “As we got with Astec, we found out our guard rails were set too low and with that, we opened our guard rails up and proved that the moisture meter worked properly. That tells us that we were wasting AC all these years, because we didn't know where our moisture was.”
“We didn't know how much we were throwing out the door,” adds Bowden.
Necessary modifications like these can easily be overlooked. That’s why tracking data and creating an archive is essential.
With the Astec IntelliPac Moisture System, a key feature is its comprehensive data logging functionality. The system records virgin aggregate composite moisture levels, enabling operators to track and analyze historical trends.
By providing operators with the ability to make informed decisions and adjustments in real time, the IntelliPac system contributes to a more efficient and cost-effective asphalt production process and higher-quality end product.
The industry is changing, and data will take us further than before
Not too long ago in the industry, many lab technicians or operators would rely on their gut and experience to adjust moisture levels. Now, that won’t cut it.
“When I was trained the first time, when it rained, we'd go in there and punch up moisture,” says Bowden. “I've actually found out during this testing that our moisture was actually higher than what I was trying to do all these years. And we always wondered why we chased AC. Once we installed this sensor, our AC is consistent.”
“I wish I had this product 20 years ago because it's been a headache chasing the AC up and down all the time, trying to get it right,” adds Strickland.
What’s next for Dunn Construction? Not only are they keeping the IntelliPac Moisture System at the flagship site, but they are also putting it on their other plants as they continue to look for ways to enhance their operations.
“We fully integrated this system into our operations, and I truly believe It's going to pay for itself,” says Strickland. “It's a lot easier on us here at the Dunn Construction.”
Strickland and the Dunn Construction team aren’t interested in keeping this a secret. They can see this helping out plant operations throughout the industry.
“It would be beneficial for anyone in our industry to get this product - it is a game changer,” adds Strickland. “All you have to do is input your safeguards and the IntelliPac Moisture System will do the job.”
The IntelliPac Moisture System sensors can be tailored to meet the specific needs of your plant. Connect with us today to learn more.
Find Astec product availability nearby
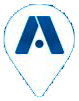